Where 11 000 Lada's are "made" every year
Chronicle of the Bakony Works in Veszprém until the change of regime (1938-1989)
On July 1, 1949, a terse announcement appeared in the Hungarian Gazette under the number 304/1949, which reported that "The Government decided to establish a national company under the name of Veszprém Metal Processing Ltd. under Article 8 of Act XXXVII of 1948.
The company is based in Veszprém.
Object : Generally the manufacture, assembly and trade in all kinds of hunting or hiking equipment.
Duration : Indefinite period.
The Minister of Heavy Industry is responsible for the company (Council of Ministers Decision No 117/1919)."
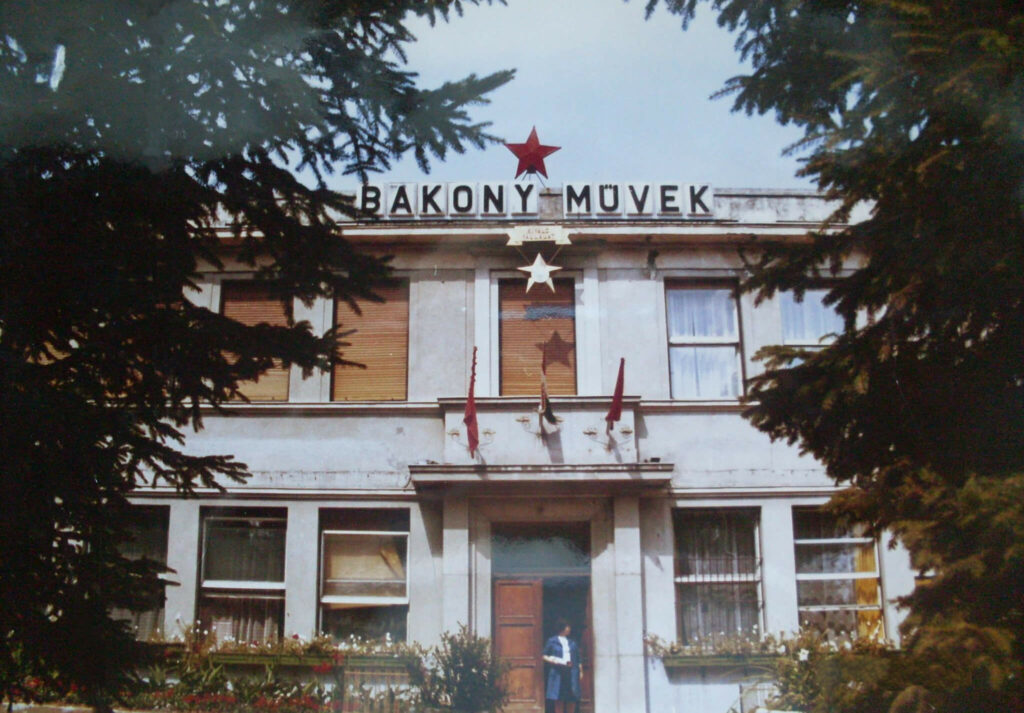
The 1970s - Image source: facebook / Bakony Művek
At the time, similar announcements were being made; they could have done so: in a country that had not yet recovered from the ravages of war and had not yet recovered from the communist takeover, such a pace and scale of innovation would have been unthinkable, but by then all obstacles to mass expropriation and nationalisation had been removed.
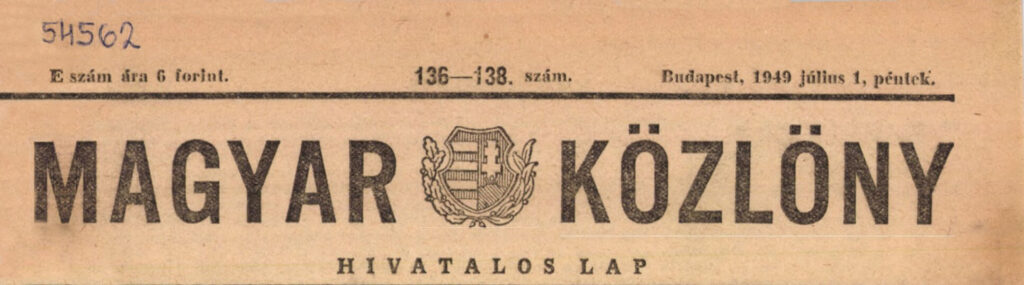
Source: arcanum
This was also the case with the Hungarian Ammunition Works Ltd. founded in 1938 by the General Directorate of the Hungarian Royal Military Material Factory in Veszprém - for the production of infantry ammunition - which, as we have read above, was baptised Veszprém Metal Processing Plant Ltd. in the new system.
The beginnings
The factory, which was dismantled and removed by the Germans in 1945, was used after the war to repair tanks for the Soviet army, with fifty people at the start and a hundred by December. After the withdrawal of the troops, the factory was used to manufacture small appliances and household utensils, and after nationalisation, ammunition production was resumed.
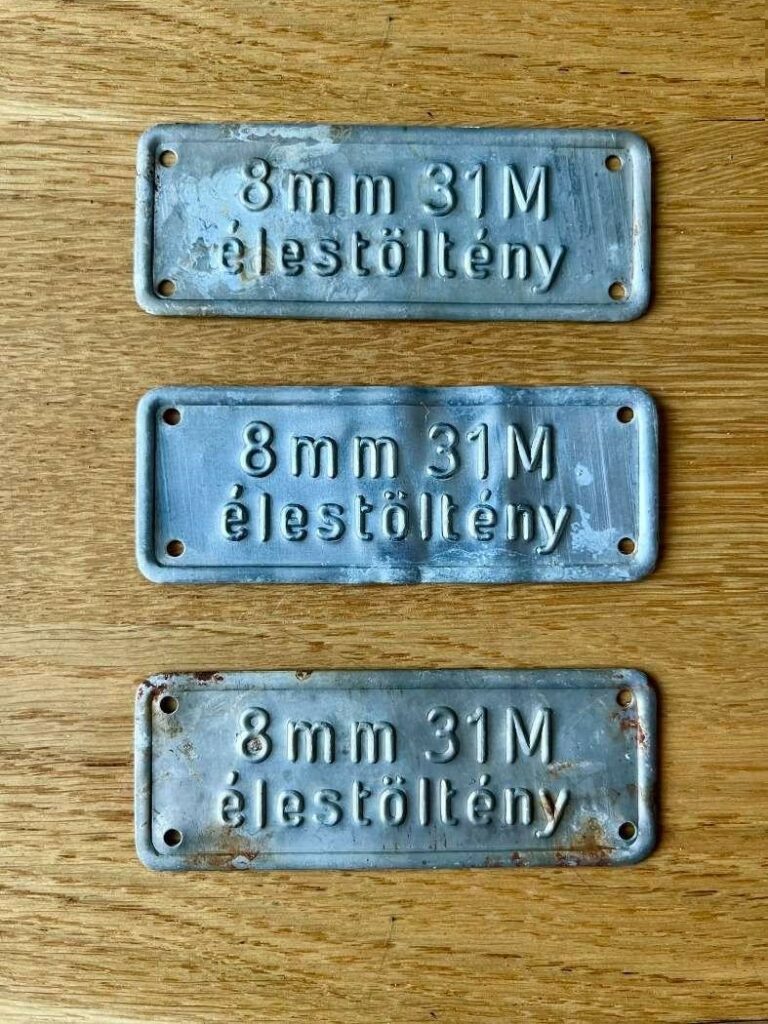
Image source: vatera
By the mid-fifties, the dwindling demand for ammunition shifted the focus of production back to serving civilian needs: small series of siphon cartridges, blade caps, lighters, locks, bicycle dynamos were produced alongside ammunition.
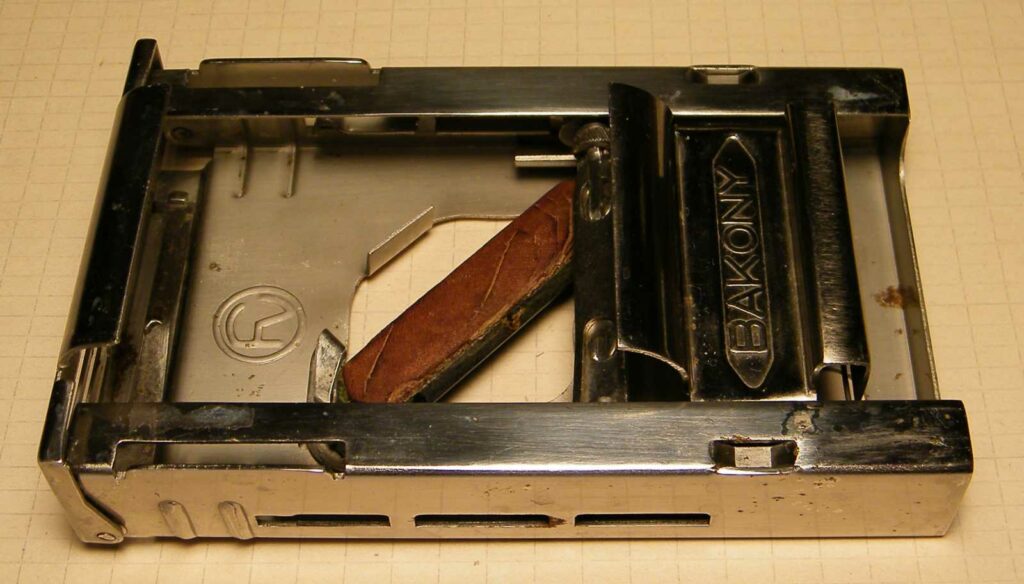
Bakony automatic razor-blade-bottom device, not yet from "Bakony-Művek" - Image source: szetszedtem.hu
This is how the next - not to be underestimated - decade or so passed, in which the second main profile - the manufacture of electrical goods - slowly seemed to evolve. (The first - less publicised - remained the manufacture of ammunition.) In 1967, for example, more than 400 different products were manufactured in the factory, where the continuous daily production was dominated by automatic circuit-breakers, voltage regulators, switches, sockets and plugs, but 'incidentally' they also produced some twenty-two million soap cartridges for Répcelak, around two million lipsticks for the beauty industry, and the 'Bakony' blade-bottom device continued to enhance the reputation of the factory, among many others.
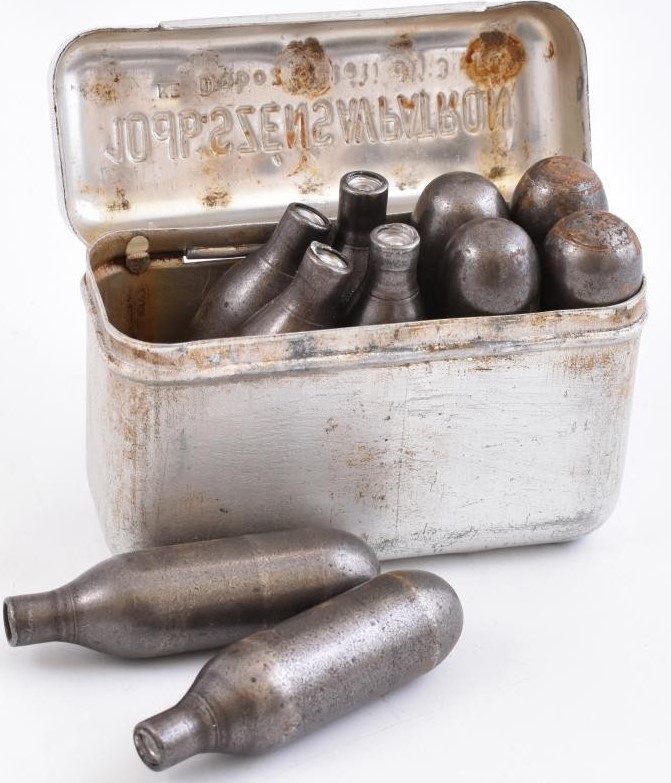
Image source: darabanth.hu / karap_norbert
In the same year, 1967, the company was headed by a new director - Béla Koltai, who had been recruited directly from DIMÁVAG in Miskolc, where he had previously spent fifteen years in the same position at the head of the Borsod-based heavy machinery manufacturer. In an interview in October, Koltai had already spoken as a matter of fact about his involvement in the Soviet FIAT programme, but negotiations had also been held with Volswagen and Renault. At the same time, the entire production of motorcycle and bicycle lighting equipment was taken over from Egri Finomszerszámgyártány, and preparations were also begun for the relocation of the spark plug production unit in Budapest to Veszprém (formerly Autóvillamossági Felszerelések Gyára, still earlier Pesterzsébeti Győrógyertyár, which was transferred to Bakony Művek as a 'self-clearing' factory in 1968 by state decision.)
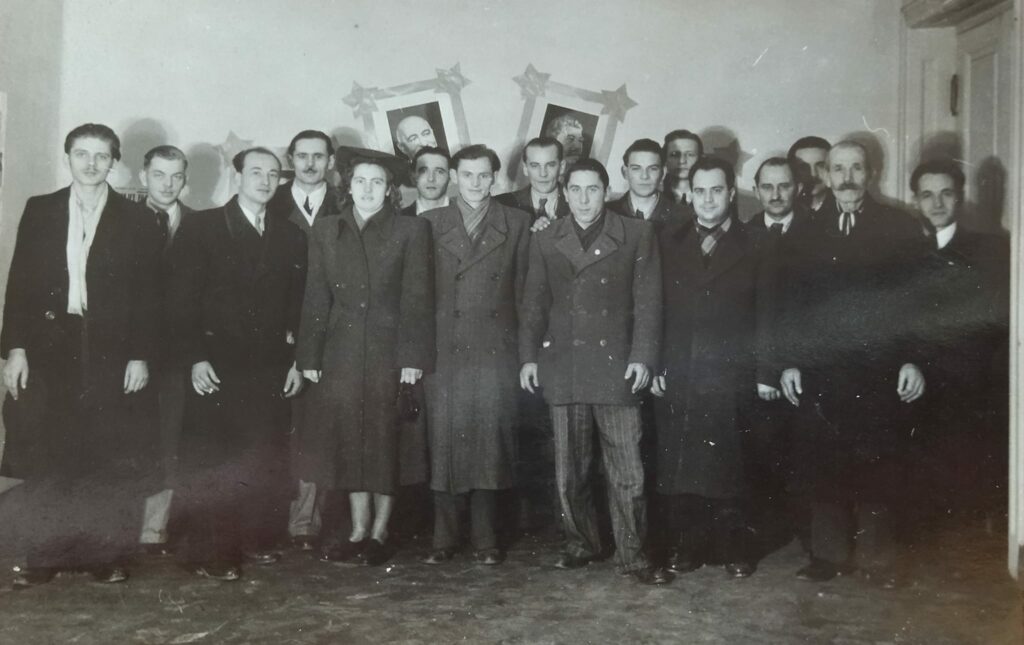
A group of workers at the Veszprém Metal Processing Plant, sometime in the 1950s - Image source: facebook / Veszprém in old photos
The company officially took the name Bakony Fém- és Elektromoskészülék Művek on 1 January 1968.
A digression: the FIAT-VAZ contract
On 29 March 1966, Leonid Brezhnev, General Secretary of the USSR Communist Party, in his address to the XXIII Congress of the Party, urged the increase of motor vehicle production in the Soviet Union, encouraging not only the modernisation of existing plants but also the installation of new ones.
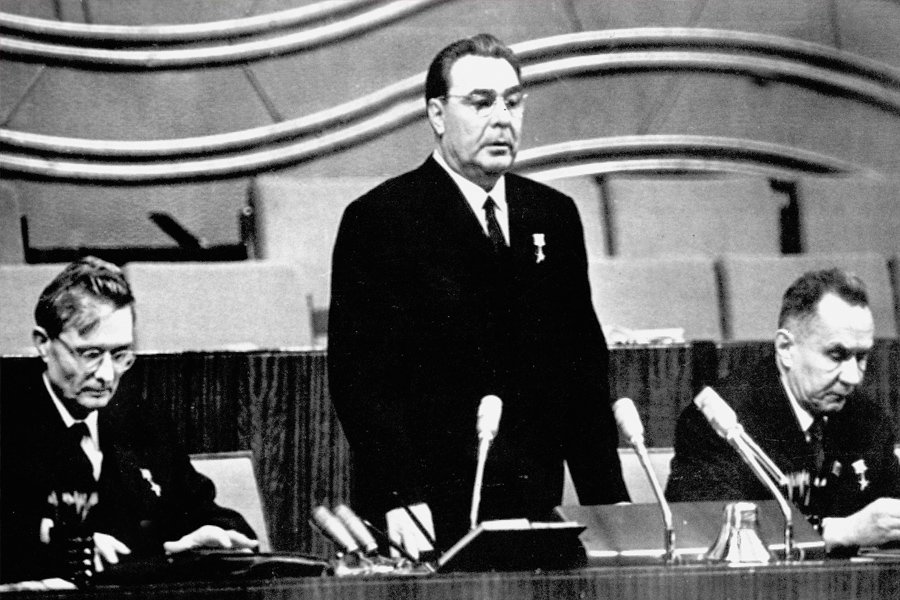
Leonid Brezhnev on 29 March 1966 at the XXIII Congress of the USSR Communist Party. On the right Alexei Nikolayevich Kosygin, Chairman of the Council of Ministers, on the left Mikhail Andreyevich Suslov, member of the Political Committee.
Negotiations between FIAT and the Soviet Union officially began on 4 May 1966, as confirmed by Tolloy, the Italian Minister of Foreign Trade at the time. The truth is that the agreement was almost finalised at that time, and it is not inconceivable that the FIAT 124 was already being developed by the factory to meet the needs of the licence.
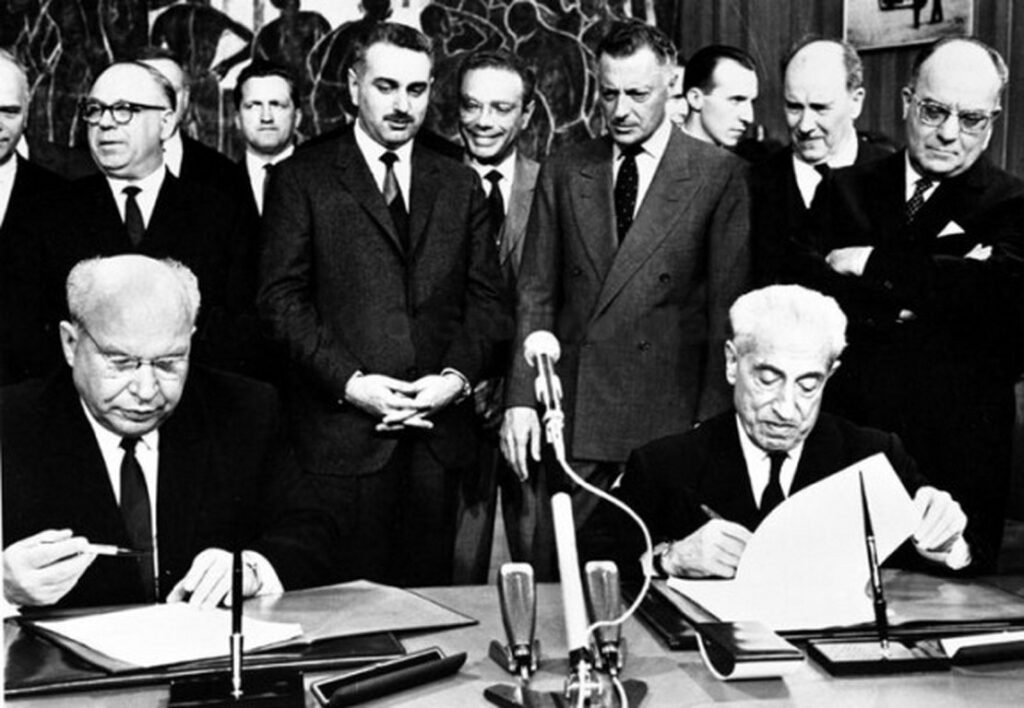
1966 – Alexander Tarasov Minister of the Automotive Industry of the Soviet Union and Vittoria Valletta, President of FIAT at the signing of the contract in Turin. - Image source: wikipedia
The FIAT 124 made its debut at the Geneva Motor Show in March 1966, and in August 1966 a framework agreement was signed between the Soviet Union and the factory, which provided, among other things, for the construction of a large plant for the production of 800,000 cars a year in Togliatti, formerly Stavropol, in Samara County. The contract, which also included the purchase of licences, was of historic importance for both parties: the largest contract ever signed by FIAT was also the largest single contract signed by the Soviet Union with a foreign company, worth USD 800 million.
The first VAZ 2101 rolled off the production line in Togliatti in 1970.
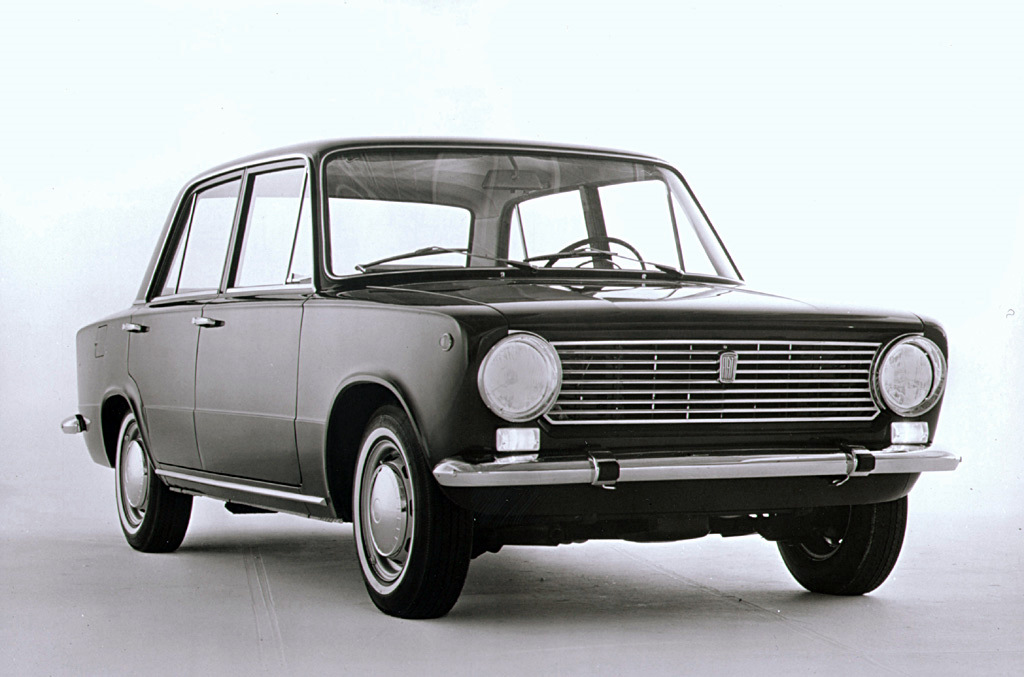
FIAT 124 Berlina 1966 saloon - Image source: fiat124.xoom.it
The long seventies (1968-1980)
In the life of the company, now called Bakony Művek, the period between 1968 and 1970 was, apart from investments, mainly about profiling. In addition to the HUF 20 million (roughly two billion in today's value) investment in the construction industry at the Veszprém site, machinery was purchased for HUF 150 million (roughly HUF 14.5 billion in today's value) from the Soviet Union, Czechoslovakia, the GDR and the USSR, but major suppliers included Switzerland and France. At the same time, a new plant was built in nearby Várpalota, outsourcing the production of around 4,000 locks and lock parts a day.
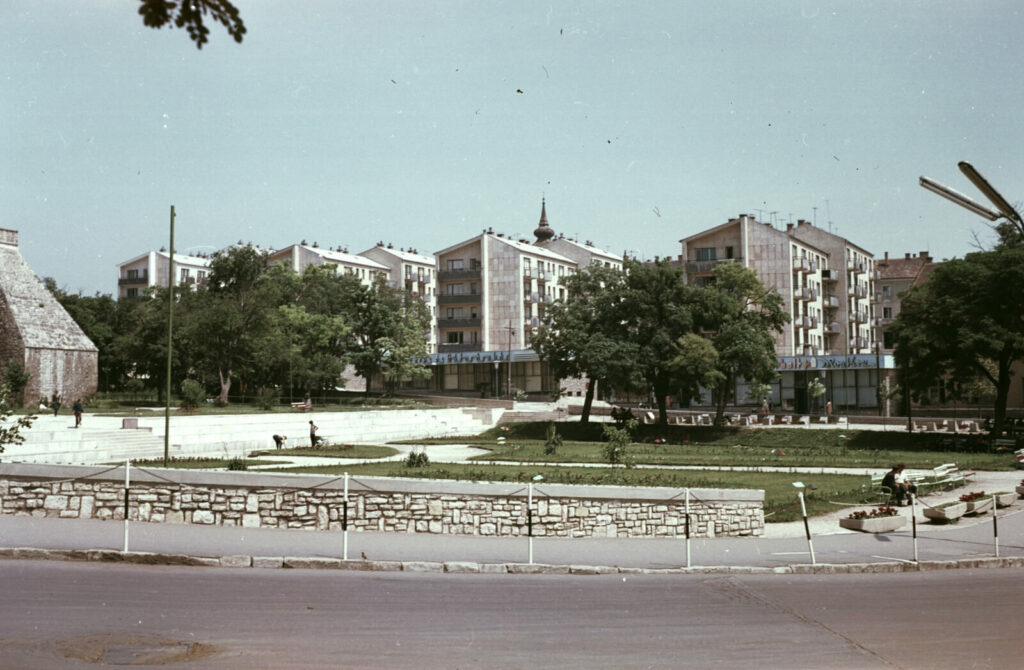
Hungary, 1969 Várpalota, Hunyadi Mátyás (Main) Square, Táncsics Mihály Street in the background. - Image source.
During the same period, the number of employees increased from 3 000 to 5 000.
The production of VAZ products started in 1970, at the same time as the birth of the first Zsiguli. In the first year, some 35,000 electrical kits were delivered, consisting of a steering lock ignition switch, ignition distributor, low and high-pitched horn pair and a complete window washer system.
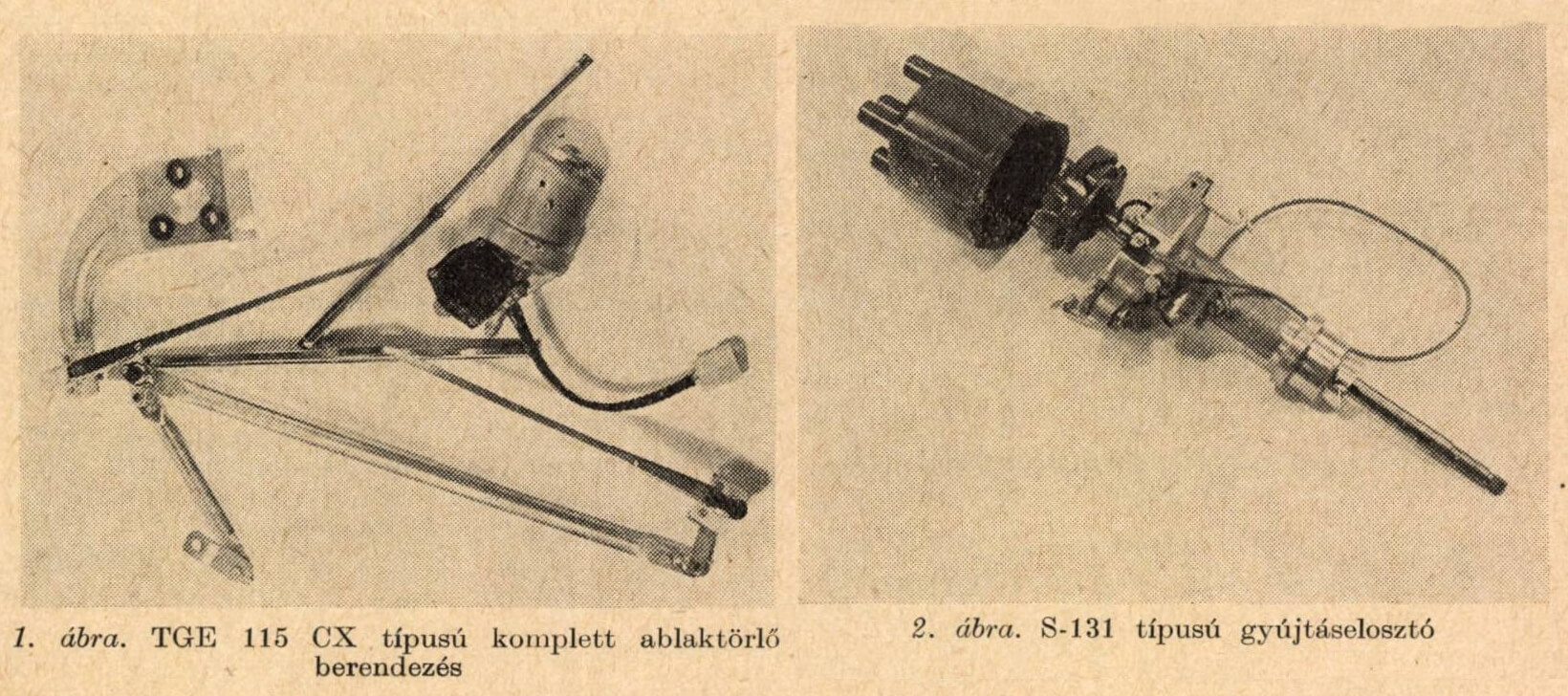
Image source: arcanum / Villamosság 1974 évf. page 287
In 1971 the figure was 150,000, and in '72-73 it was 300,000, which was about half of the total demand for Togliatti.
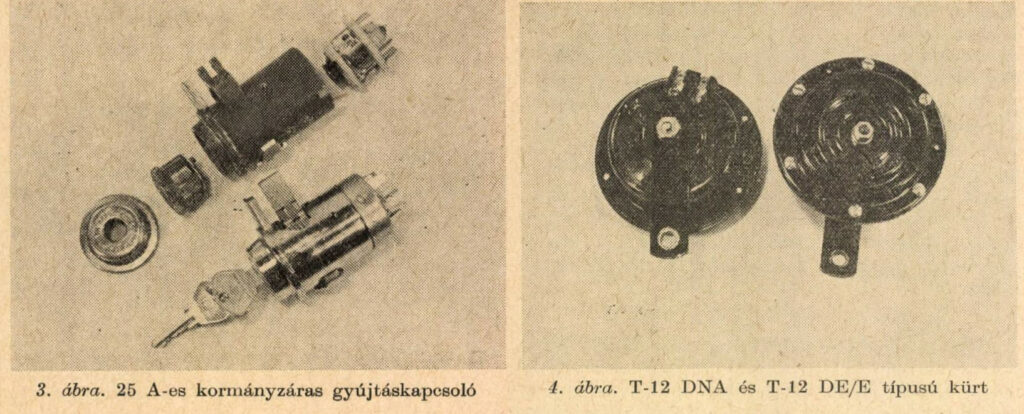
Image source: Arcanum / Villamosság 1974 vol. pp. 287-288
Less common information from these times is that in the framework of the so-called MOPED program, under a KGST agreement, the production of Simpsons, Barkas and some other East German machines and equipment, including flywheel magnets, was transferred from the GDR to Veszprém.
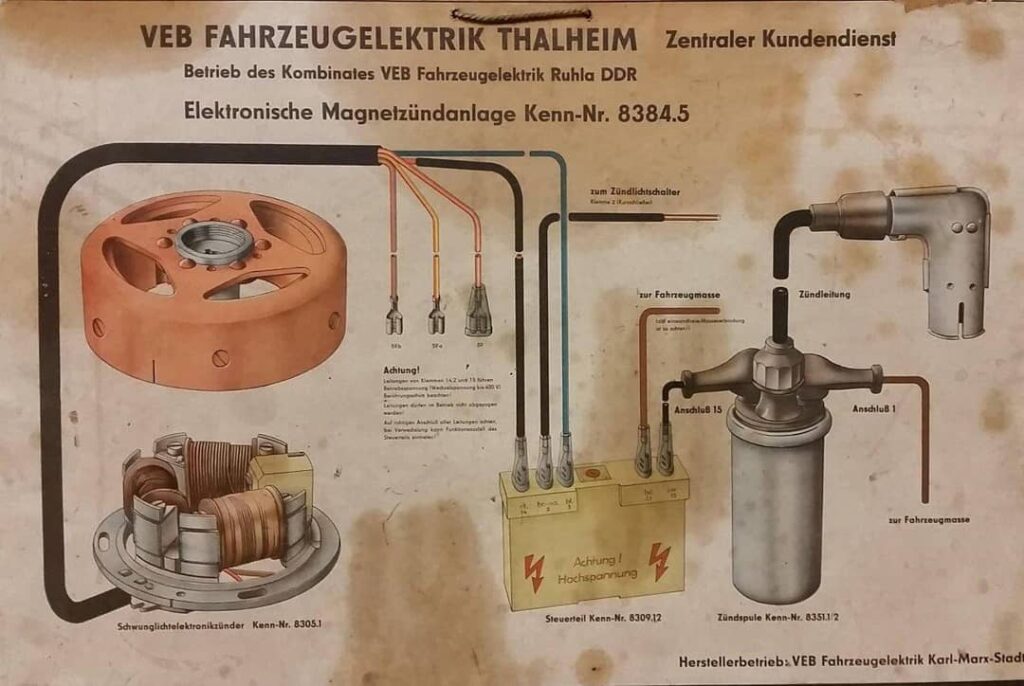
A still original GDR version, probably for Simson SR-1 - Image source: facebook / Zweirad Schubert
At the beginning of the decade, Béla Koltai was succeeded by János Bergou for a short period, and in 1975 by Gyula Sós, who later continued his career as Deputy Minister of Industry (1985). (Sidebar: his son Csaba Sós, European bronze medallist, world championship fifth place swimmer, coach, university professor. Since 1990 he has been vice-president of the Hungarian Swimming Federation, and since the end of January 2017 he has been the captain of the Hungarian national swimming team.)
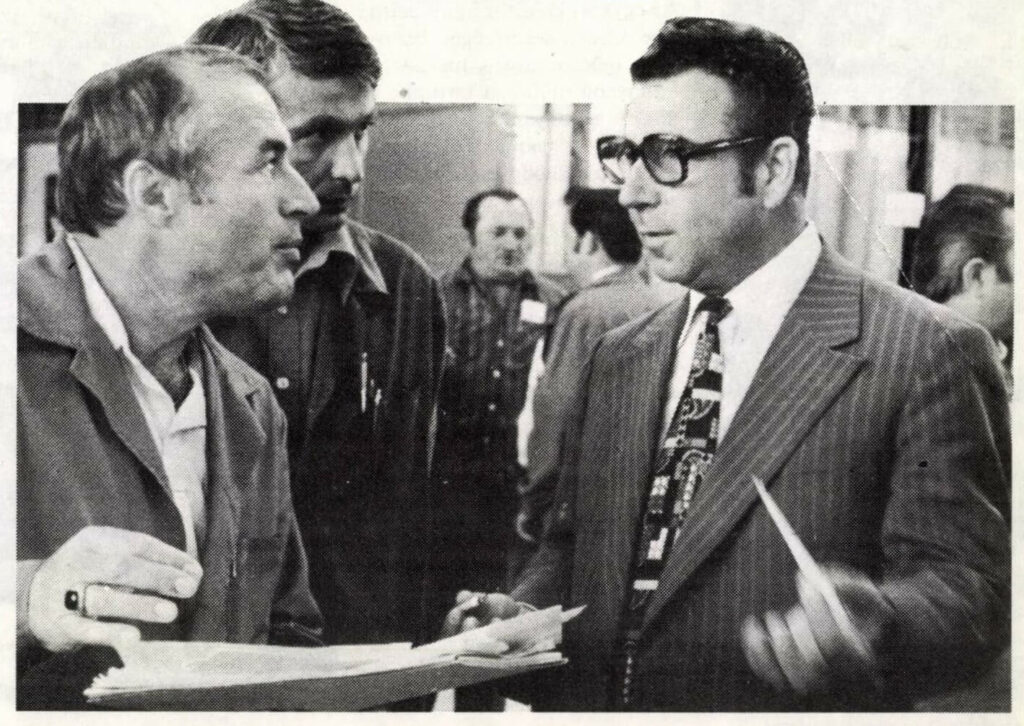
On the right Gyula Sós, director of the company in its "golden age" - Image source: Arcanum / Ötlet 1982 Aug.
By 1977, the number of employees had increased to 6,100, 55% of whom were women.
By 1979, the number of kits delivered to Togliatti was around 400,000, but by that time the horns for Moskvits and Kamazs were also being made here, as well as ignition distributors, wipers, horns and horn regulators for the Polish Polski 126p, in a production run of around 200,000 a year. In addition, Zaporozsec, Dacia and, from '82, Zastawa expanded the range of products served.
Ikarus was the biggest customer in the domestic market.
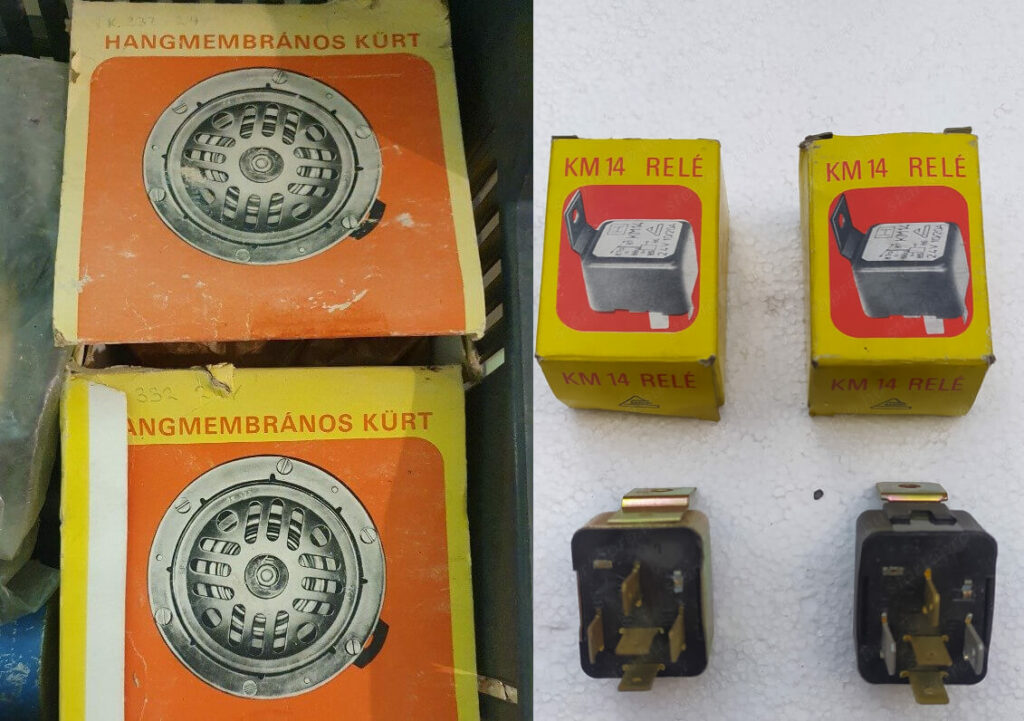
If 24V, then Ikarus - Image source: vatera and startapro.hu
The success also boosted other players in the domestic economy: the Bakony Works' initial 40-501 tpd of imported raw material consumption had fallen to 8-91 tpd by this time. The Salgótarján Metallurgical Works, the Lenin Metallurgical Works and the powder metallurgical plant of the Industrial Assembly and Machine Works were also among the major suppliers.
Bakony Művek was by then the largest employer in the town and operated in seven other locations in the county - Várpalota, Tapolca, Keszthely, Devecser, Dudar, Kerta and Mezőlak. In Budapest, in Kertész Street, a brand store awaited customers.
By the early eighties, the company had achieved what it had set itself a decade earlier: Bakony Művek was listed on the market as an internationally leading automotive and automotive power supply manufacturer. (In the second half of 1979, an article [Hungary, 1979, September] mentions 11,000 Ladas a year received in exchange for parts from Bakony Művek.)
Another detour: the other business sectors
1. The Schrack circuit breakers
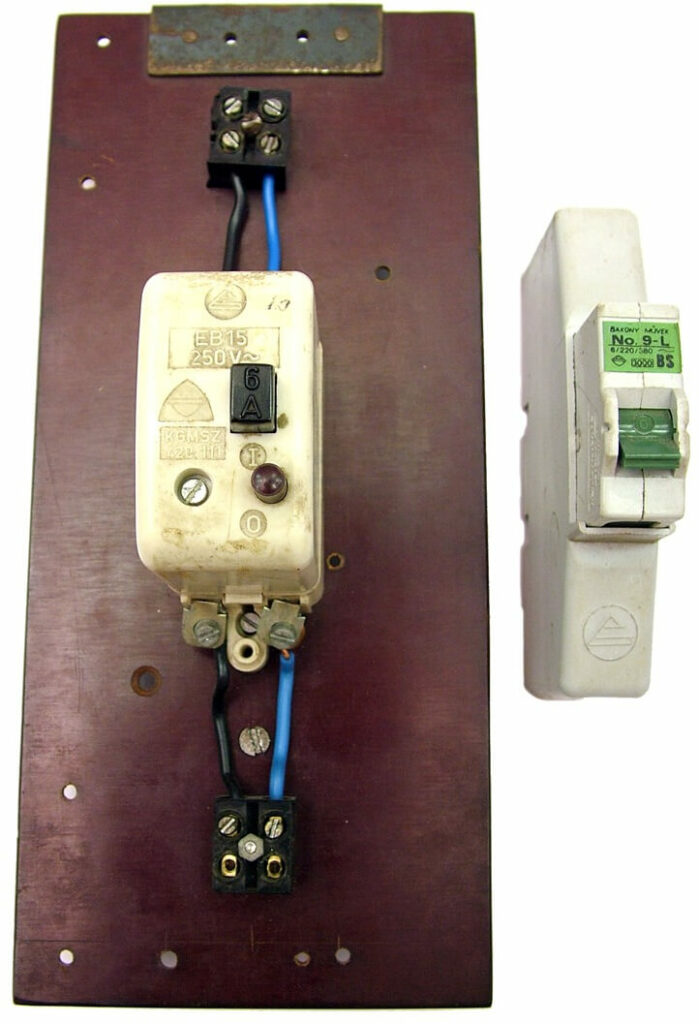
The old EB and the new - Schrack BS circuit breakers from Bakony works
By the end of the sixties, as we have written before, Bakony Művek was dominated by the production of electrical goods. Household circuit breakers, which were by then rather obsolete as one of the leading products, had been in production for just ten years, but the burdens imposed on the company by the start-up VAZ cooperation did not allow for the development that seemed inevitable. Then came the Austrian company SCHRACK, with whom, after a year and a half of negotiations, a contract was signed in mid-1969, sharing the production rights for their modern and high-quality circuit breakers with Bakony Művek on rather favourable terms. The Schrack circuit breakers were well established and in demand on the world market, a significant part of which was from then on served by Bakony Művek.
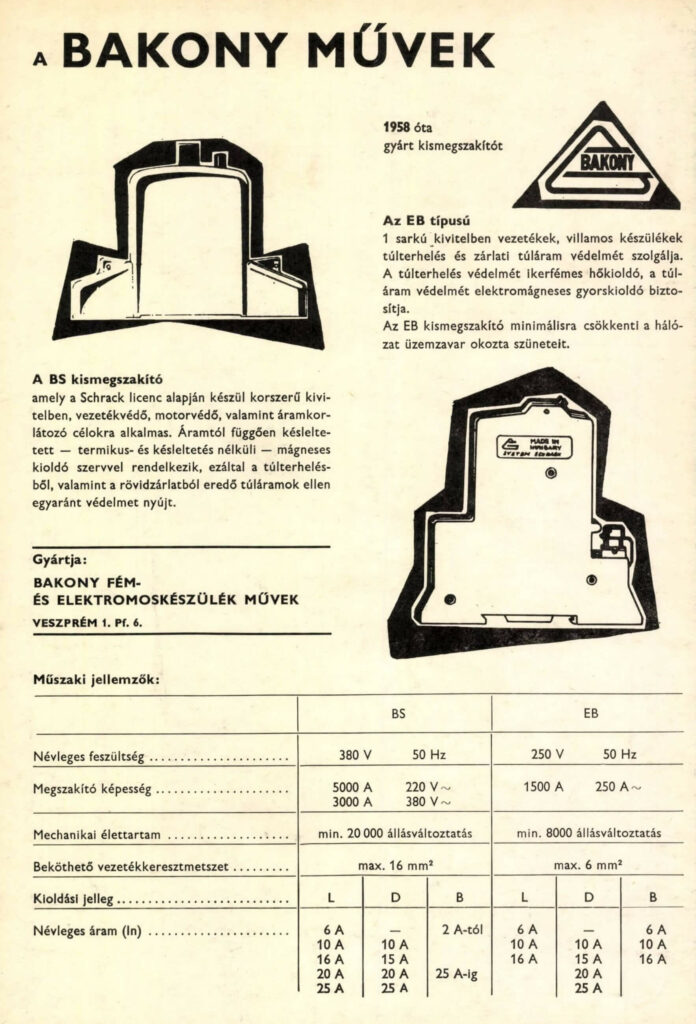
Source: Arcanum / Villamosság 1974, page 287
The contracting parties divided up the markets between them, so that in addition to the CIS countries, we also supplied Albania, China, India, Pakistan, Iraq, Iran, Syria, Egypt, Lebanon and Cuba.
Production began in the second half of 1970, and the finished products were marketed under the sign "Schrack manufactured under licence by Bakony Művek".
2. Bosch Industrial and Installation Equipment
Bakony Művek paid great attention to increasing productivity. It was one of the first in Hungary to use the 3M method, which contributed greatly to the fact that by 1980 productivity levels had doubled compared to 1970.
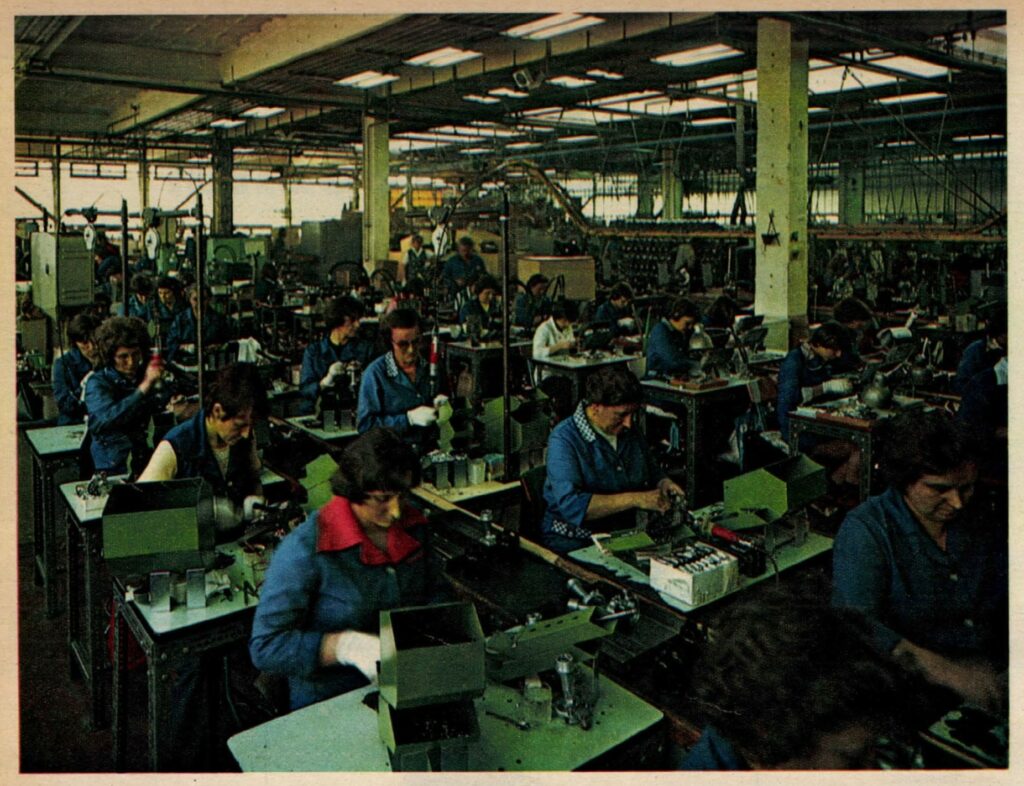
Source: Arcanum / Autó-Motor April 1977
Of course, the working method itself, based on motion analysis, would not have been enough for success without the appropriate technical and technological background, so mechanisation and rationalisation of processes were also constantly on the agenda.
At the beginning of 1975, the factory signed a licence agreement with the West German company Bosch for the production of 32 different products for the mechanisation and automation of assembly, which, in addition to meeting its own needs, also found their way onto the world market, developing into a separate business sector. By 1976, a completely new production line had been built to assemble the ignition distributors in Kispolsk, but by the following year, some 100 million batches had already been sold on the market. (One of the first foreign customers was the Electrical Appliance Factory in Großhain near Dresden, where from then on generators for Wartburgs and Trabant cars were produced on the assembly lines of Bakony Művek.
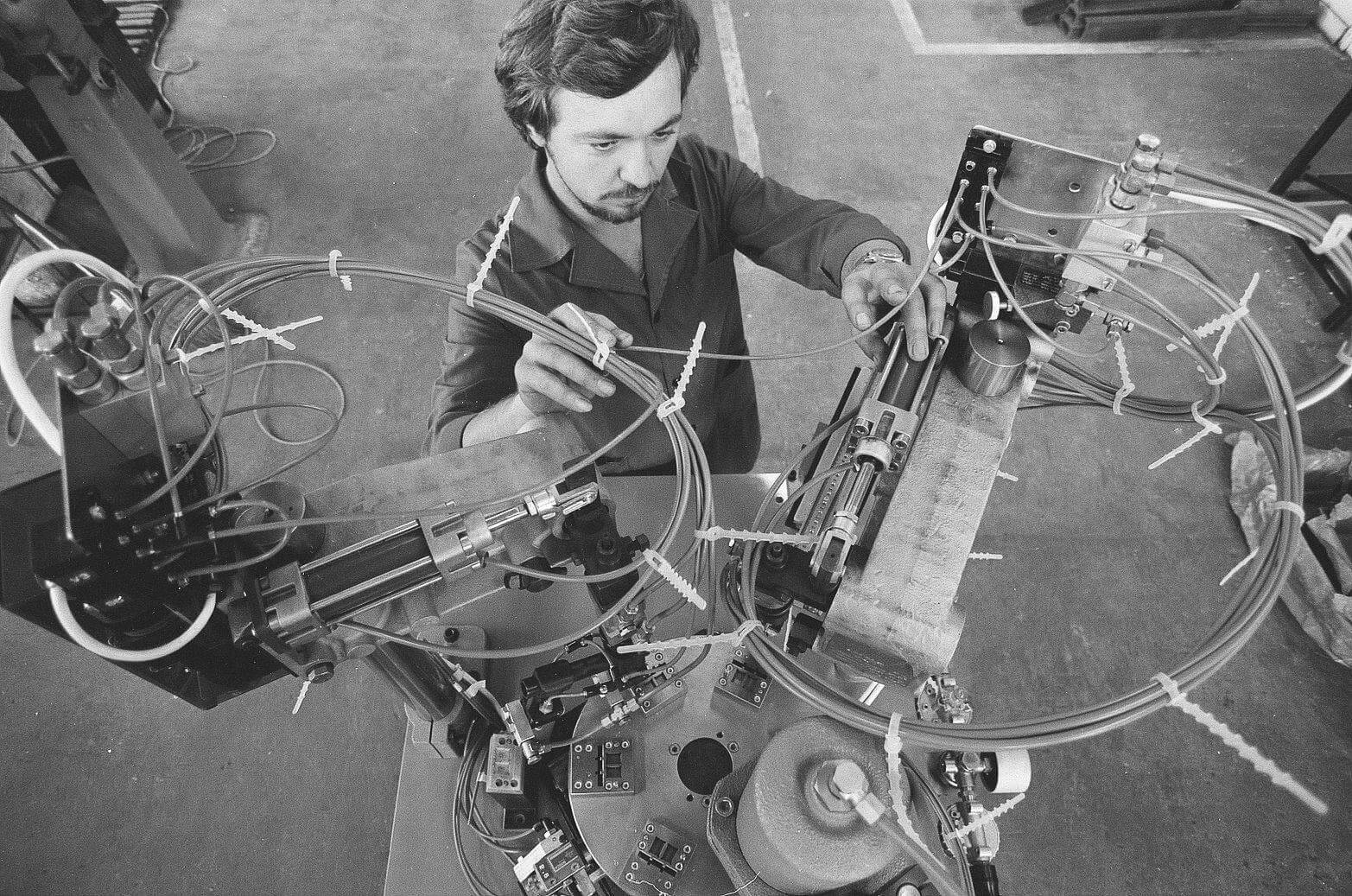
Image source: arcanum / Népszava press photos 1981
How much the Schrack and Bosch business should not be underestimated is illustrated by the fact that by 1981 the production of car parts accounted for 401T3T of the company's total turnover, and the number of people employed in this segment 'only' about 371T3T of the total workforce.
3. The spark plug business
TIMKOR
The year 1968 was the year when the Pesterzsébet Spark Plug Factory became the property of Bakony Művek as a self-clearing factory, based on a state decision. As the only plant of its kind in Hungary, even then, about 10,000 candles (two million per year) were being burned in the kilns every day.
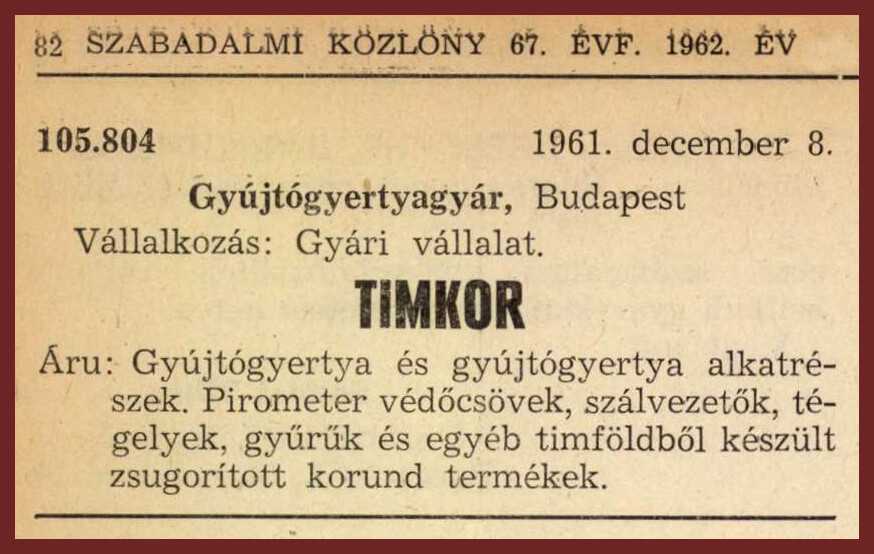
Patent registration of TIMKOR from 1961 - Image source: Arcanum / Patent Gazette 1961
At the following year's MTESZ exhibition in Veszprém (1969), the candles were already presented as Bakony Művek products on the stand under the name TIMKOR (TIMKföld+KORund), and negotiations were started with VW, Bosh, Simca and the American Champion. The Veszprém product was already being marketed in Italy under the name "Safari".
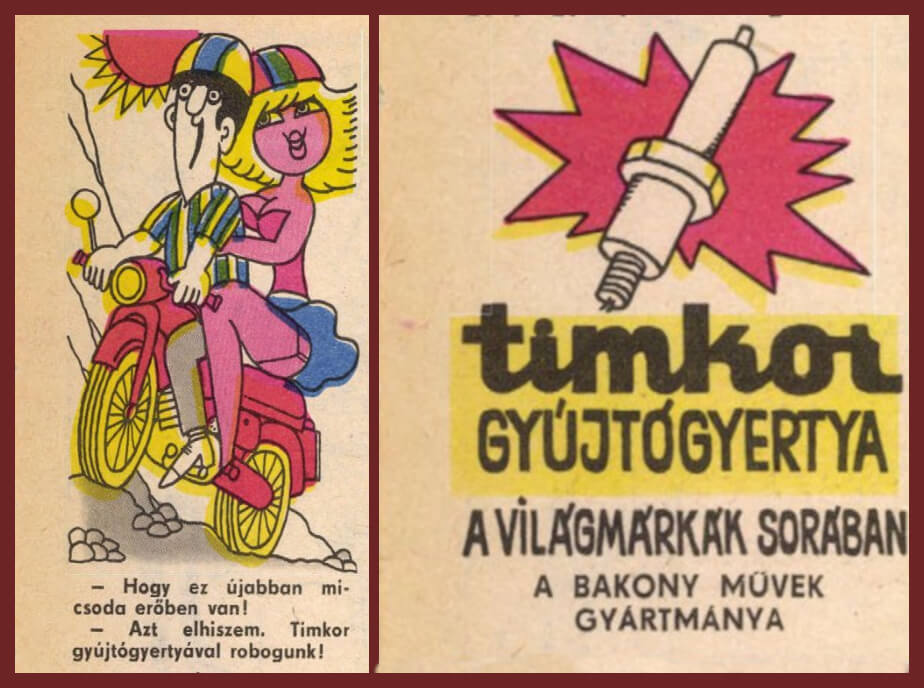
Timkor candle advertisement from page 13 of the 9 August 1973 issue of Ludas Matyi - Source: Arcanum
At the same time, the candle factory in Budapest was facing a constant shortage of labour, and orders were often delayed.
At the same time, work began on the relocation of the capital's plant to Veszprém, but the handover of the new ceramics hall, originally scheduled for mid-1974, was significantly delayed: the Veszprém County Council Construction Company left the work half-finished and did not look forward to it for a good year. As a result, the factory suffered heavy losses at the time.
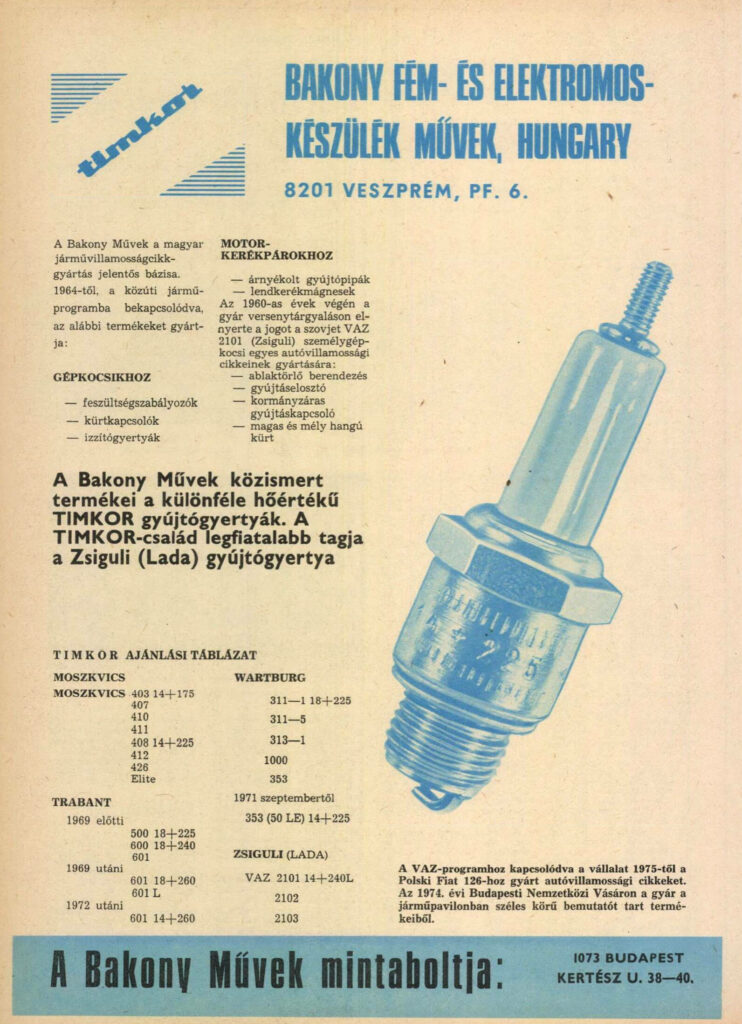
TIMKOR candle advertisement from page 30 of the 14 April 1974 issue of Magyarorszag - Source: Arcanum
The trial operation was finally launched after a two-year delay, only in July 1976, after the anomalies surrounding the project had become a national scandal.
BAKONY
The new factory was accompanied by a new "brand": the spark plugs were replaced by the old "Timkor" and introduced as "Bakony" spark plugs on the '77 BNV. The following year, more than three million of these were produced. From 1978, in-house thermometric measurements - previously carried out on candles in Moscow and Dresden - were made possible thanks to the transfer of a new laboratory, but the market did not back up the effort; it rated the product as poor.
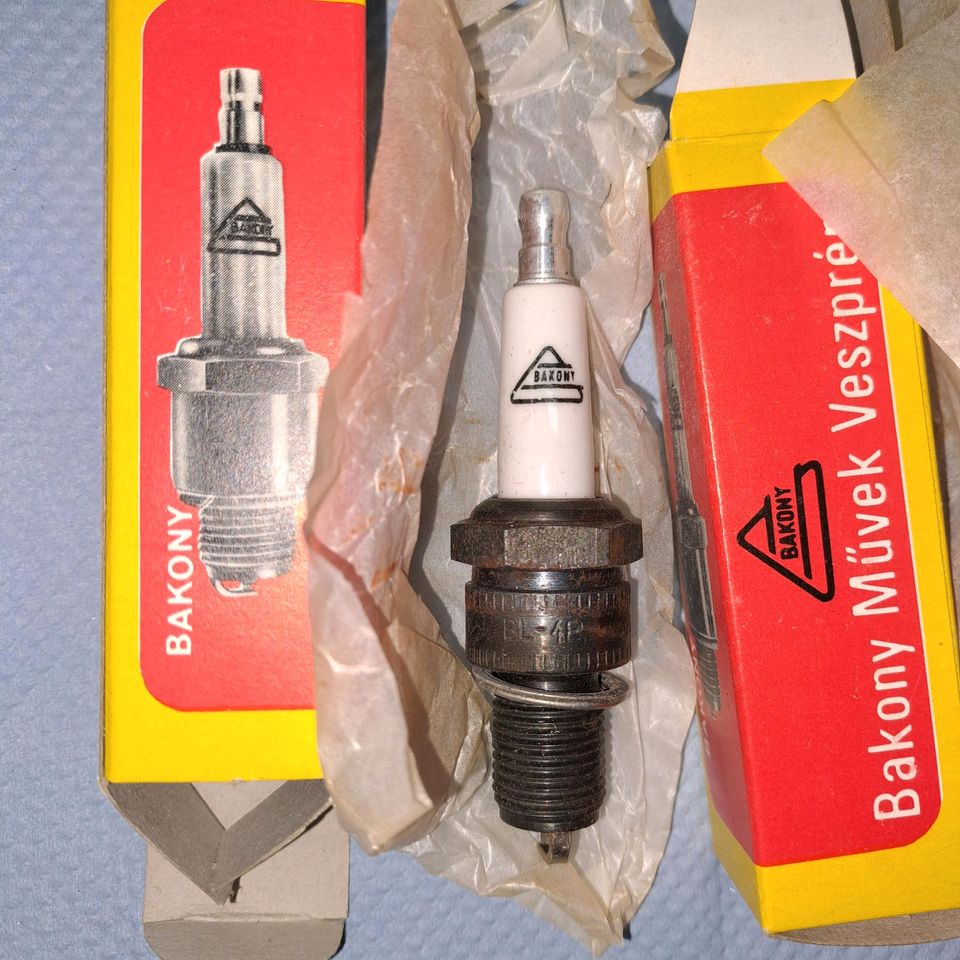
Source: ebay kleinanzeigen
In 1981, roughly 9 - 9.5 million spark plugs were sold in Hungary, of which about 7 million were imported, and of these 7 million only about 2 million came from capitalist markets (so the public was much more willing to buy GDR Isolator candles than domestic ones).
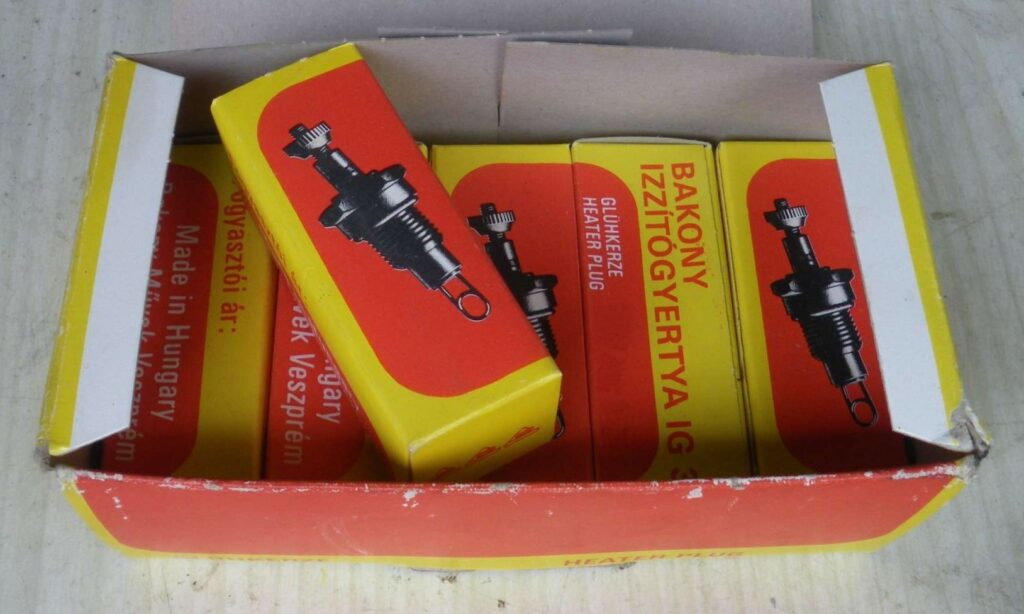
Source: csepelautoalkatresz.hu
By this time, the very outdated production lines were producing with about twenty percent(!) waste. In August 1980, Bakony Művek signed a 200 million forint (nearly 11 billion today) loan agreement with the Hungarian National Bank to modernise production.
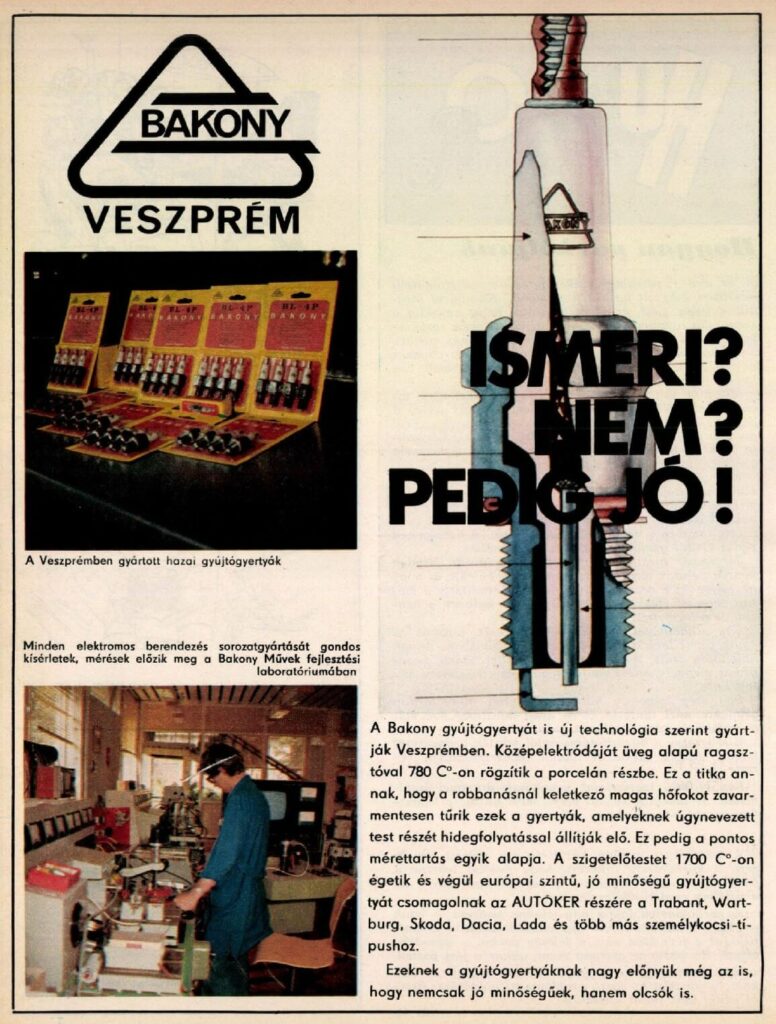
Bakony spark plug advertisement from the October 6, 1979 issue of Autó-Motor (page 62) - Source: Arcanum
It was an admission that the domestically developed spark plug industry had failed.
KLG
The upgrade was not left to chance: a licensing agreement was signed with Smith Industries, the manufacturer of the "KLG". Under the terms of the agreement, the British company provided Bakony Műv with complete candle designs, production technology, technical documentation, material recipes, inspection and testing methods, and at the same time undertook to train the workers. The contract also included the supply of the necessary equipment, machinery, measuring and testing devices.
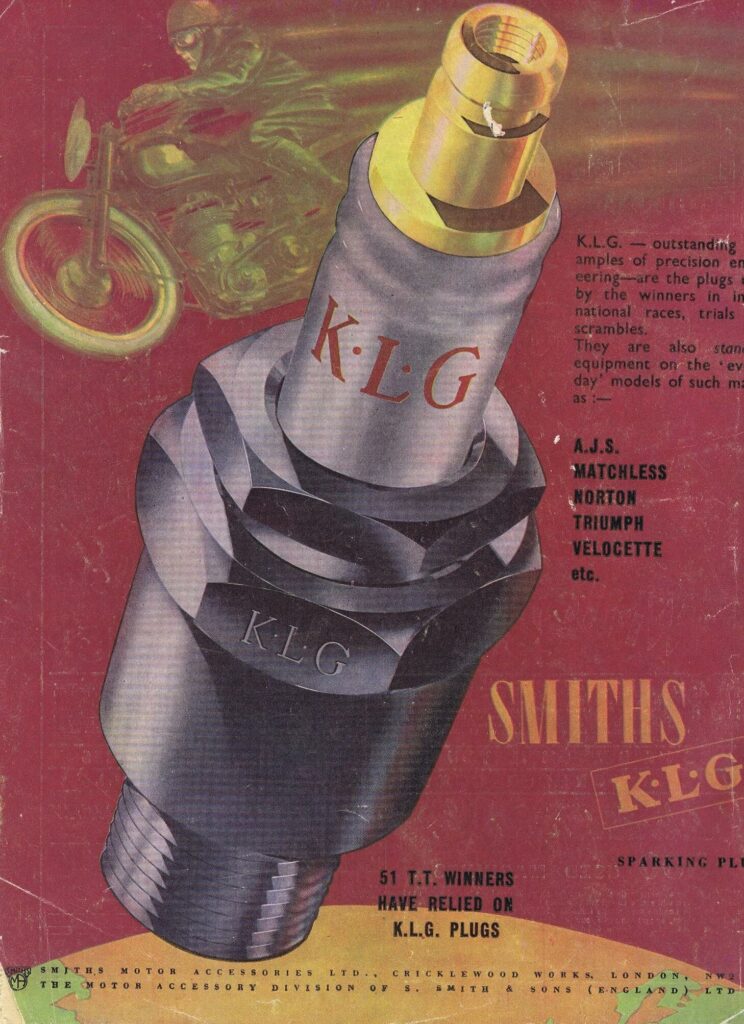
KLG advertisement from 1951 - Source: flickr / Geoff Novak
From then on, until the launch planned for March '83, the delicate parts were imported from the British partner and the production of "KLG" spark plugs began alongside the "Bakony".
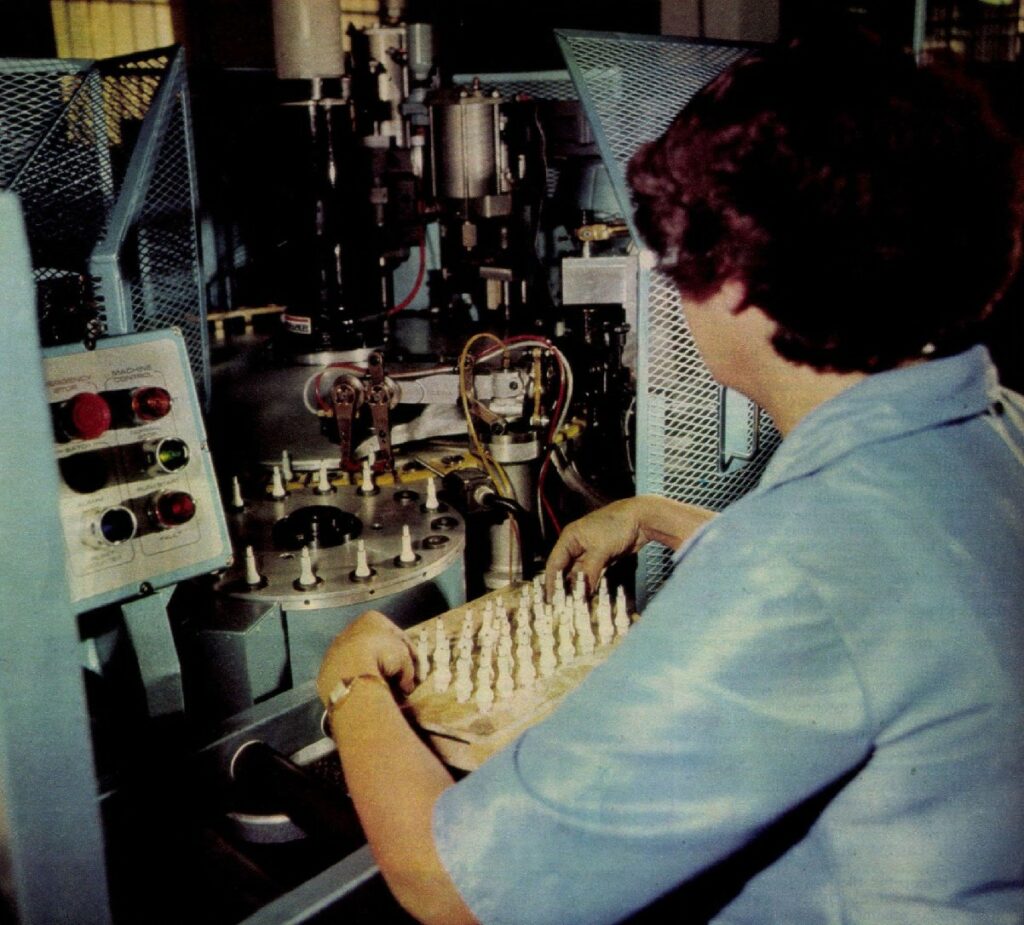
Image source: arcanum / Autó-Motor 1983 Jan 15.
The new plant was finally able to start up in November '82, at the same time as the "Bakony" candles were gradually phased out of the market.
In 1984, Bakony Művek sold around seven million of 14 different types of "KLG" candles, of which 2.5 million were sold in domestic shops, 2 million in socialist countries and 2.5 million on capitalist markets.
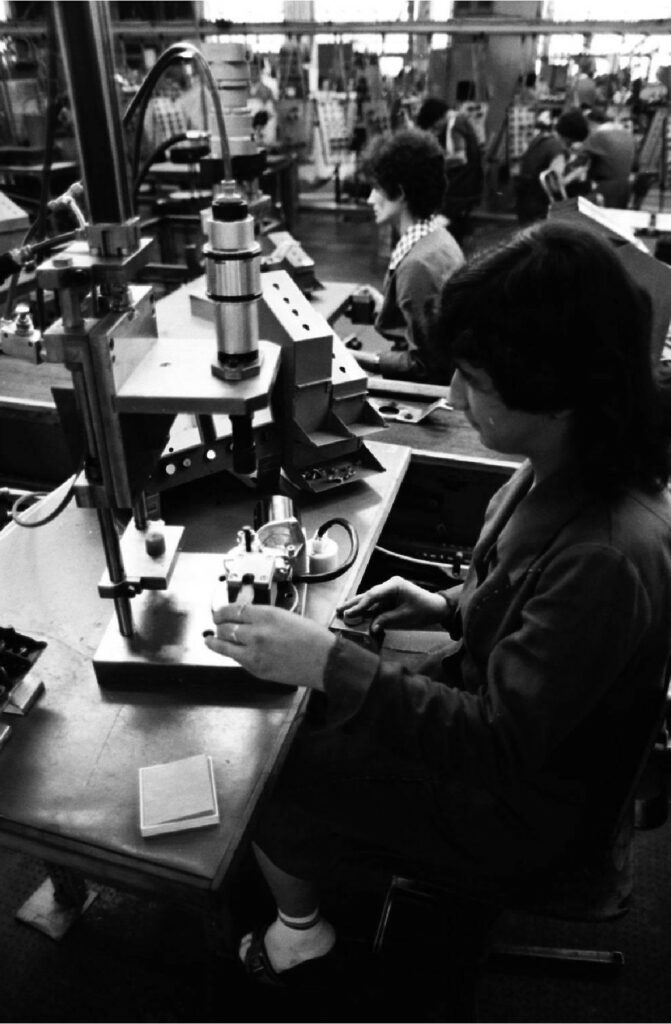
Image source: arcanum / Népszava Press photos June 1985
Yet in the next year or two, the reports of victory that had always accompanied candle-making became less frequent. The next news item to receive national publicity was that in 1987 the candle-making division was separated from the factory and continued to operate as a separate factory. The reason was probably so as not to detract from the - still - good numbers of the other divisions in the statistics.
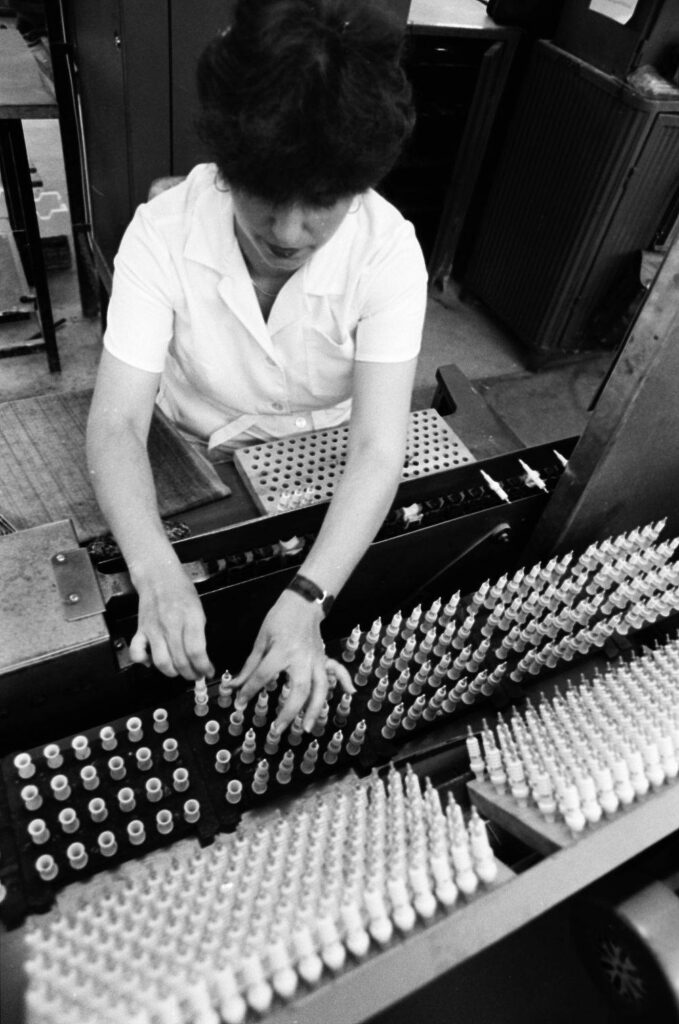
Image source: arcanum / Népszava Press photos June 1985
The short eighties (1981-1989)
Although by the early 1980s the "Bakony" spark plug and thus domestic spark plug development seemed to be failing, the other business sectors - and thus Bakony Művek - were doing very well. Soviet and generally socialist car parts exports were at their peak, and Schrack circuit breakers and - especially - Bosch industrial and assembly equipment, together, were pulling the company.
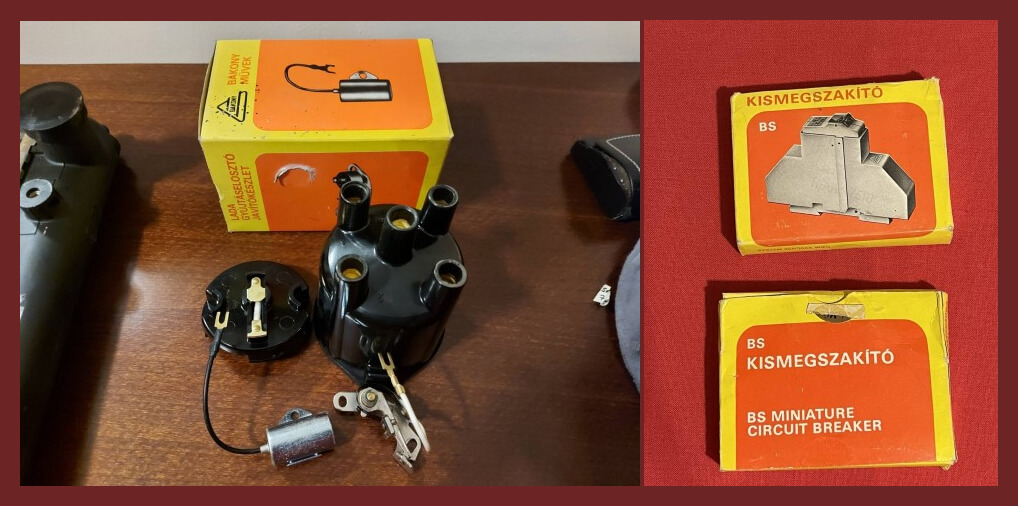
Image source: jofogas.hu
The company signed a cooperation agreement with Ikarus, the new spark plug plant was launched, the five-day working week was introduced, and a new assembly line was set up, laying the foundations for the production of Lada Samara parts.
The annual net profit in '82 was about 4.5 million forints, in today's terms, roughly 216 million forints.

Source: Arcanum / Autó-Motor April 1977
By then, however, the Hungarian economic reform was already faltering, and the inflexible industrial and trade structures in Hungary and the CIS were not even allowing the country to keep up, despite the best intentions. The supply of domestic parts was stagnant and very expensive, and there was little scope for cheaper, high-quality capital imports because of economic regulators. (Even then, about half of foreign exchange earnings were being used to repay the national debt, and foreign exchange-producing firms had very limited access to convertible funds.) Contracts concluded a decade or more earlier could not be renegotiated, even though raw material and energy prices had risen considerably during this period (at that time, about 40 1tn 1tn of total production were socialist exports.)
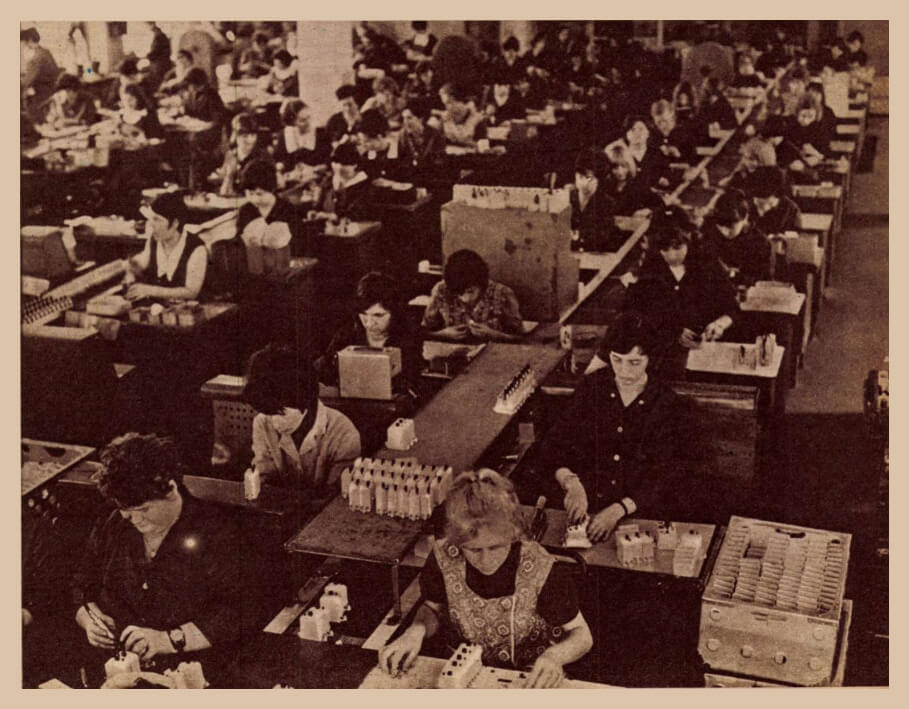
Picture from the sixties: the production of the EB circuit breakers - Source: Arcanum / Flagship October 1969
In April 1985, Gyula Sós, the company's CEO, was awarded the then very prestigious "April Fourth" medal and on 27 May the government appointed him - third in line - Deputy Minister of Industry. He was succeeded by Tibor Moravetz, the former Party Committee Secretary.
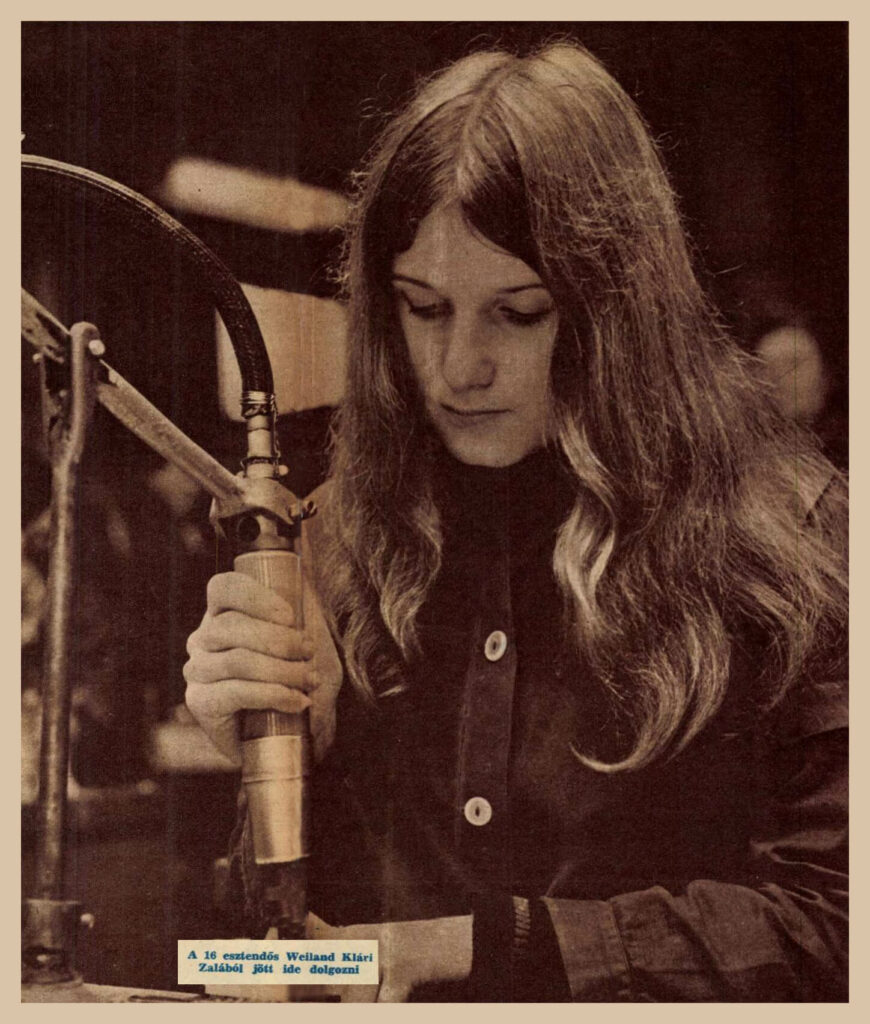
Picture from the sixties - Source: Arcanum / Flagship October 1969
In the same year (1985), the assembly and automation plant was transformed into an independent factory. They signed a contract with the Soviet Electric Motors factory and also with Moskvich, GAZ and ZIL for the supply of various PLC systems. Promising component supply contracts were signed with Daciá, in addition to the existing ones, and volumes were increased with Zastawanal and Polski 126P in Poland.
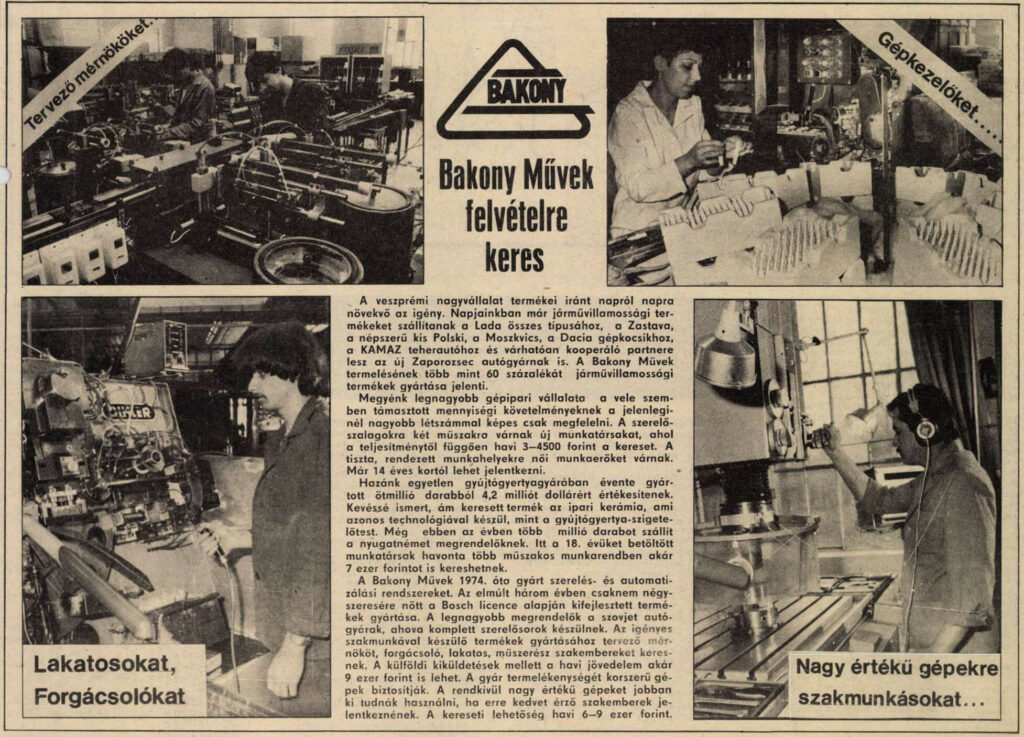
Job advertisement from the Veszprém Journal of 12 September 1987 - Source: Arcanum
From the outside, everything may have seemed to be fine, but as socialist models slowly but surely evolved, expectations changed. The fact that discontinued and new products had to be produced in parallel for years caused many problems, with the result that the 'old' models lost the advantage of high volume production, while the 'new' models took years to ramp up.
The machinery and production equipment were worn out due to the high but insufficient investment, their 14% was close to zero and the staff shortages were becoming increasingly pressing, despite the fact that the company's productivity had increased by 59 % by 1985 compared to 1980, and wages were higher than the legal requirement.
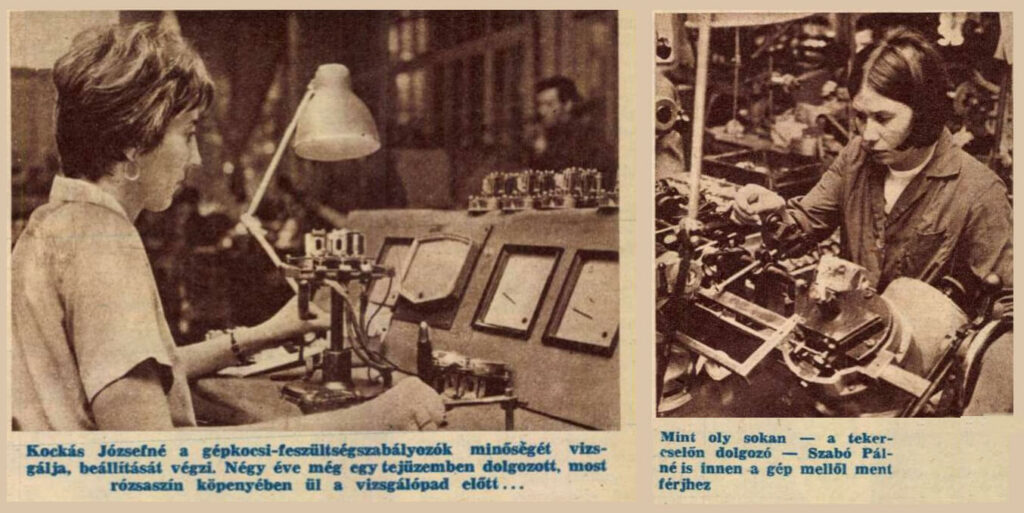
Picture from the sixties - Source: Arcanum / Flagship October 1969
Although the company's 5% capital import exposure was very low, imports in foreign currency were only possible after a serious licensing process, if at all: the framework was approved late and import licenses were delayed. By 1986 the figures had deteriorated, production and therefore employment were stagnating; the accumulation of semi-finished products was also a serious problem.
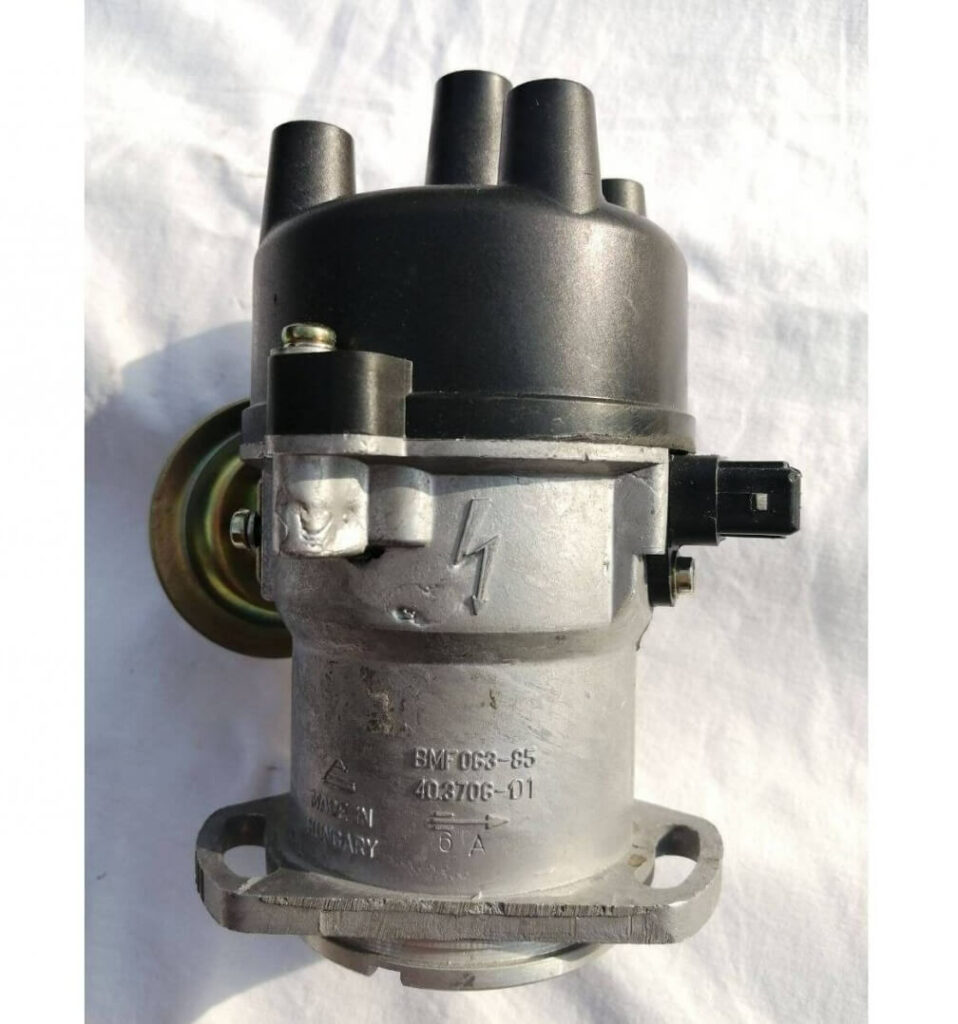
The self-developed Lada Samara ignition distributor - Image source: jofogas.hu
The production of the self-developed Lada Samara ignition switch could not start on time, the production of carbonic acid cartridges had to be forced to stop at the Kerta plant due to a lack of raw materials, and the production of bicycle lighting products was stopped due to ongoing staff shortages.
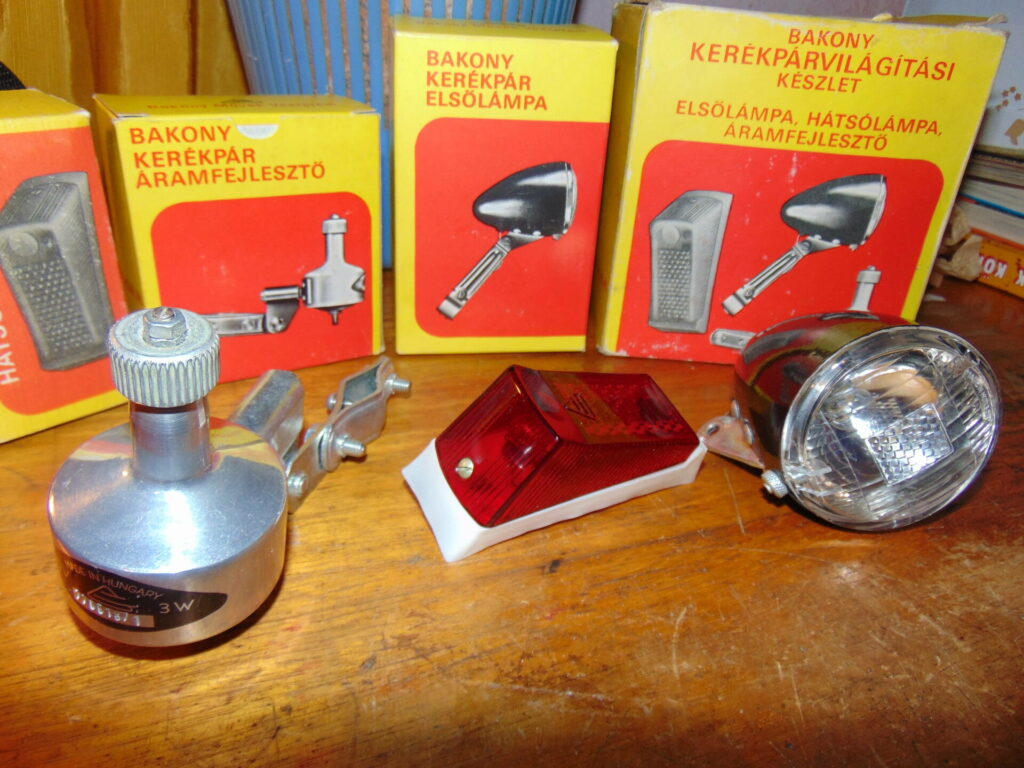
Bakony Művek's bicycle lighting products in the 1980s - Image source: www.chaharsoogh.ir
To their credit, the problem was not with them, but with the system. The economic decision-makers and players knew that the existing structure of the CSTO was unsalvageable and that it would have taken years to reform it, but that neither we nor the surrounding countries, which were also severely under-resourced, had the time.
On 23 October 1989, the change of regime was symbolically achieved: the Republic was proclaimed.
In the seventies and eighties, there was a saying in Veszprém that there were three types of people living in the city: those who worked, those who are currently working and those who will work at Bakony Művek.
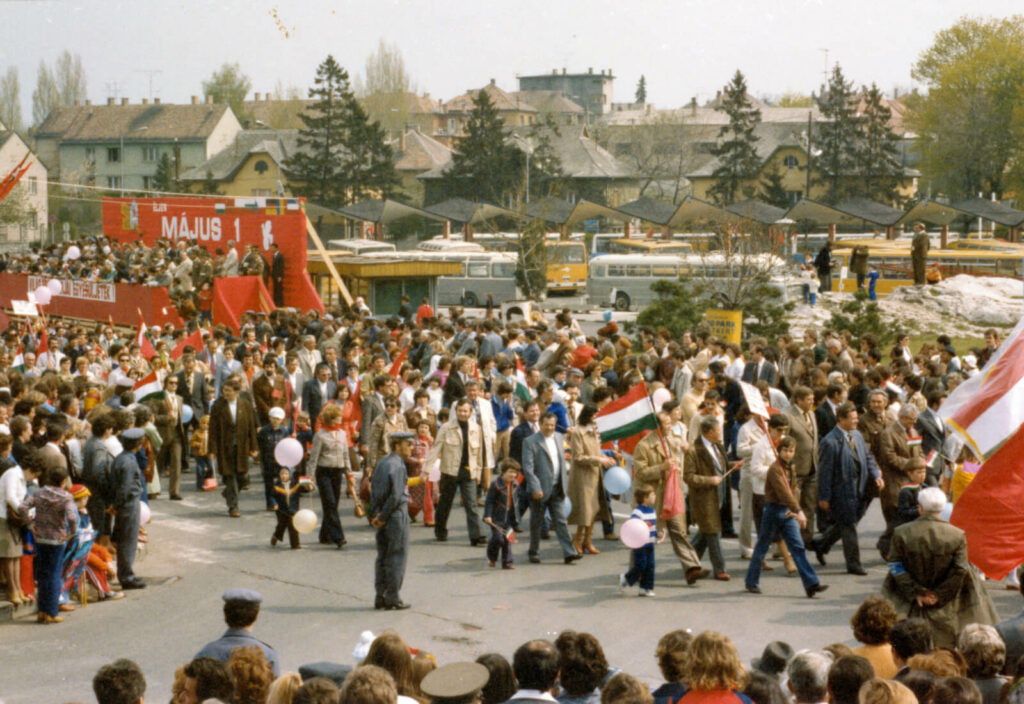
1980, Hungary,Veszprém, Jutasi (Liberation) Road, May Day parade, bus station in the background. - Image source: 70641 Fortepan / Sándor Joó
And indeed: in its heyday, the company with its 6,500 employees was the largest employer in Veszprém and the largest engineering company in the county. Even in 1990, when the system collapsed, the company employed 4,000 people.
In the mid-1980s, the cooperation was worth 10,000 Lada cars a year, but the Poles also paid in cars (126P). The company thus added around 16,000 cars a year to the Hungarian fleet.
The Bakony Művek survived the regime change, albeit with difficulty, and its history stretched until the bankruptcy in 2007. We will return to this fascinating period, which has taught us many lessons, in a later article.