1979 - The "combined" upload - 1
The theory of a revolutionary Hungarian patent
1979 Augustand Novembertwo papers on the same topic were published in the Car Engine in which - as time has proved - the truly revolutionary Hungarian patent, the on combined top-up reported. The first article, about the ALPINE, which was already in practical use in the BMW 528i, and the second, about the the technical content of the construction walk around in detail. Since it is logically and historically more justified, the articles are republished in reverse chronological order. here read more)
So below are the papers on the "combined filling" protected as a Hungarian patent later published, but here it is still the piece numbered one. Retrieved from November 1979 writing The work of Dr Győző Kiss, then Deputy Scientific Director of the Road Transport Scientific Research Institute.
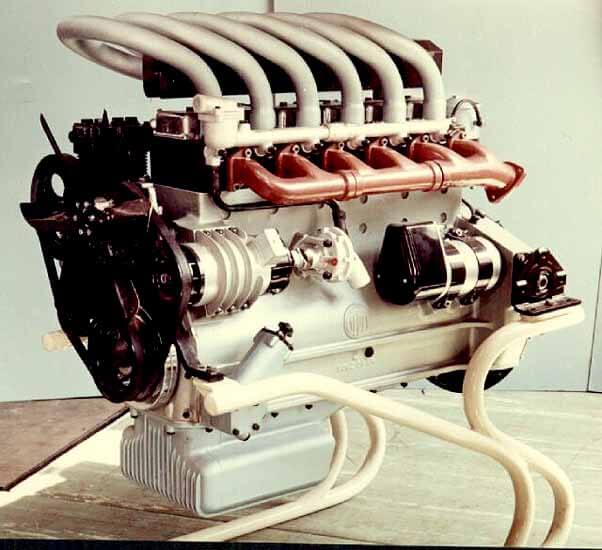
Application of Gyula Cser's world-first invention (intake manifold and resonance charging) on D-614 Csepel engine
Image source: automobilizmus.hu
♠
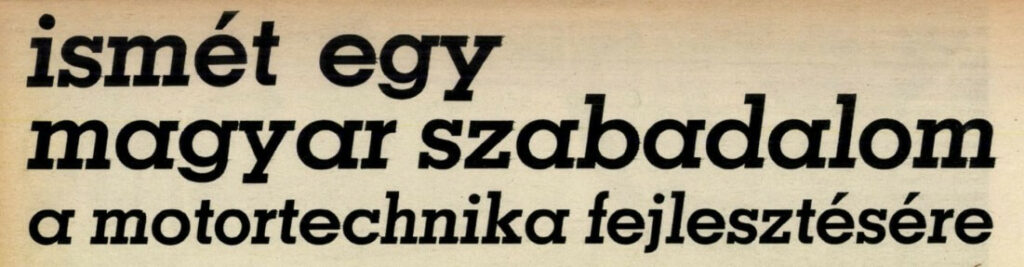
Recently, the success of combined uploading has been reported in several Hungarian newspapers and dailies, and in the 1979/19 issue of AM we also read about one of its interesting applications. At that time we reported that the top model of the BMW Alpina was made using this Hungarian invention. We concluded by returning to this important invention, which was the brainchild of five Hungarian mechanical engineers - IMRE ANNUS, GYULA CSER, SÁNDOR FLÓRIÁN, GYÖRGY HORVÁTH and FERENC KOCSIS - the result of his ingenuity, his work. Following our first news item mentioned above, we asked Dr. Győző Kissour engine technology expert, to provide our readers with more detailed information.
Developments in motorisation, the international energy situation and ever stricter environmental standards are also posing major challenges for vehicle manufacturers. In the field of resources in particular, the development of engines of classical design to meet demand is becoming increasingly problematic. This is reflected in the many different ways in which they are being sought, the most worthwhile of which are briefly outlined below:
- variation of fuels (methanol, hydrogen, propane-butane, etc.),
- equipment to reduce harmful components in the exhaust gases (thermal reactor or afterburner, catalytic converter, exhaust gas recirculation system),
- the rotary crank engines,
- the stratified mixture engine (FORD PROCO) and the pre-chamber version (HONDA CVCC),
- outboard engines,
- steam engine,
- STIRLING heat engine,
- gas turbines.
Each is trying to find its way in its own technical, economic and geographical context.
At the same time, the basic aim of all solutions is to ensure engine-side conditions for good performance, good driving dynamics and environmentally friendly operation, and I do not wish to emphasise these to the detriment of safety, economical and modern handling and maintenance features as an additional requirement.
The above requirements must be met without increasing or substantially increasing the external dimensions and weight of the engine. Power, as the most important parameter, can be increased by the first obvious solution: increasing the engine speed! This approach is mainly followed in the case of passenger car engines, where nominal speeds of up to 6000 rpm are not uncommon.
In terms of mass, this is less feasible for larger engines, and sooner or later high revving car engines will reach a point where the revs cannot be increased economically and safely!
Another solution is to get more fuel into the cylinder in the time available, with the right mixture, but this requires more air, which the engine can follow less easily with the suction effect of the piston.
The logical solution is to use the previously known boosting, or overboosting by further increasing the boost pressure. In these cases, the supercharger - blower or compressor - injects more air into the engine cylinders than the engine itself can draw in from the environment, thus allowing more fuel to be burned or the temperature level to be reduced.
Top-ups are generally seen as a performance-enhancing technique, a somewhat one-sided view. Supercharging is indeed one of the most effective means of increasing performance, but it can also reduce heat flow and fuel consumption. In addition to its advantages, there are also some problems with the use of turbochargers (turbocharging = the turbocharger-compressor is driven by a turbine powered by the engine exhaust gas and its shaft is not mechanically connected to the engine shaft).
It follows from the principle of the turbocharger:
- as engine speed increases, the amount of air delivered increases almost in direct proportion or more, while at the same time
- the higher the engine speed, the more exhaust gas, the faster the turbine spins and the more air the compressor delivers.
Internal combustion engines do not need air or fuel mixture according to this effect, but rather:
- requires more fuel when the engine is started and when the first gears are engaged, and then
- to achieve the torques required at higher speeds.
At low revs, the turbocharger delivers little or no air, so the engine operates like a classic naturally aspirated engine. If we now dispense with this and increase the amount of fuel, then the harmful components in the exhaust gases increase due to the unfavourable mixture formation, and fuel consumption increases in the same way, to mention only the most important ones.
To eliminate these undesirable effects, experiments are being carried out to ensure that the charger is not tuned to the maximum engine speed, so that it reaches the air delivery value required earlier. The harmful high pressure at higher speeds is corrected by a control valve. This solution unfortunately leads to energy loss!
The other way forward is dynamic charging, which has been used for racing cars and racing motorcycles. The idea is that, if the intake manifold is sized correctly, the pulsating motion generated by the piston's sequential suction and the self-reflux of the air column in the intake manifold can be coordinated!
The column of air thus induced to oscillate, entering the cylinder at the right time, increases the amount of air flowing in during the suction stroke.
The Institute for Automotive Research, then known as the Institute for Vehicle Development, was already working on suction pipe systems for dynamic charging in the early 1960s. The positive experience gained in improving engine parameters gave rise to the idea of combining the two solutions with a turbocharger to compensate for the shortcomings of the supercharger, particularly at low speeds. This in fact gave birth to the idea of combined supercharging, which is the essence of the invention mentioned in the introduction.
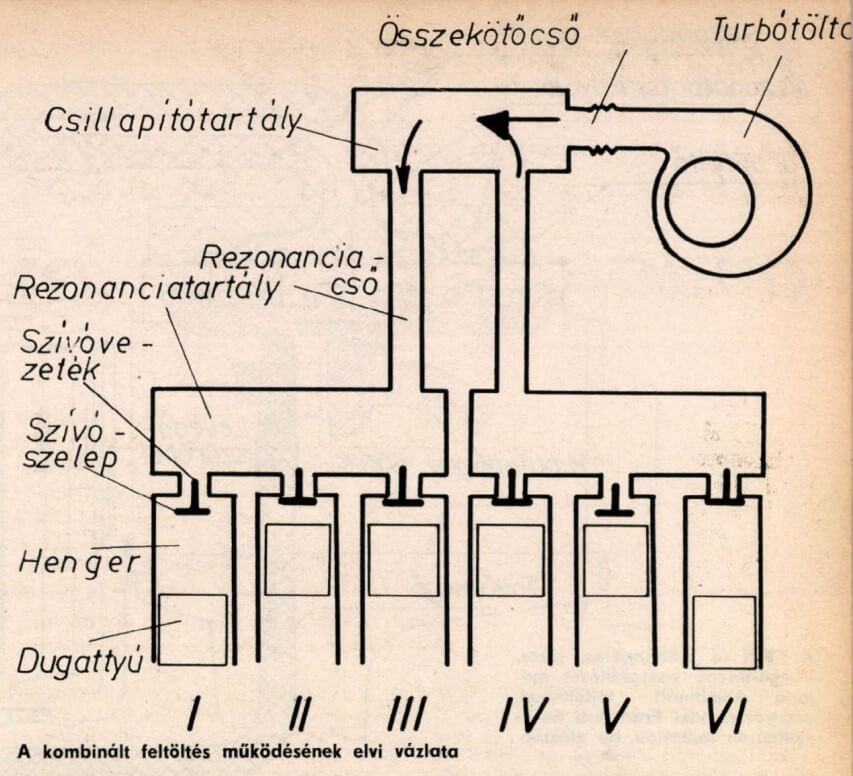
The idea was excellent, but the implementation was more difficult. It immediately became apparent that the necessary tuning for low speeds would have required geometric dimensions that would have caused serious problems of installation space, and the relatively large size at high speeds would have increased the work required for excitation, as well as the engine's consumption. The idea and then the application of the resonator tank solved this problem in one fell swoop, becoming a crucial part of the invention. The complete construction is illustrated in the diagram below. The resonator canister makes it possible to tune the intake manifold system to the speed that the nature of the engine requires, without the dimensions substantially exceeding those of a conventional intake manifold, and without increasing the losses. To illustrate the point, let's look at the processes involved.
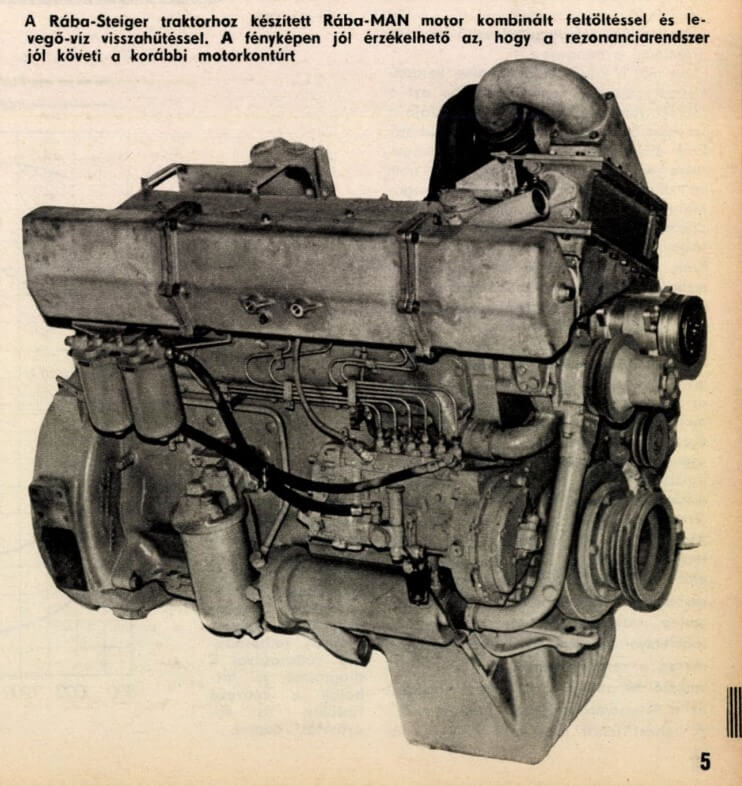
The piston pushes the excess combustion gases out of the cylinder by moving upwards and starts moving downwards in the intake manifold. During the first half of this movement, it must now not only suck in air, but also accelerate the movement of the air column, exciting the vibrations. This is obviously more
energy than the classic case of suction. In the second half of the piston's travel, the air column with the right number of strokes reaches its peak pressure. This pressure squeezes the excess air volume into the cylinder around the bottom dead centre of the piston and partly beyond. The process just described is typical of the speed to which the resonance system is tuned, otherwise known as the resonance speed.
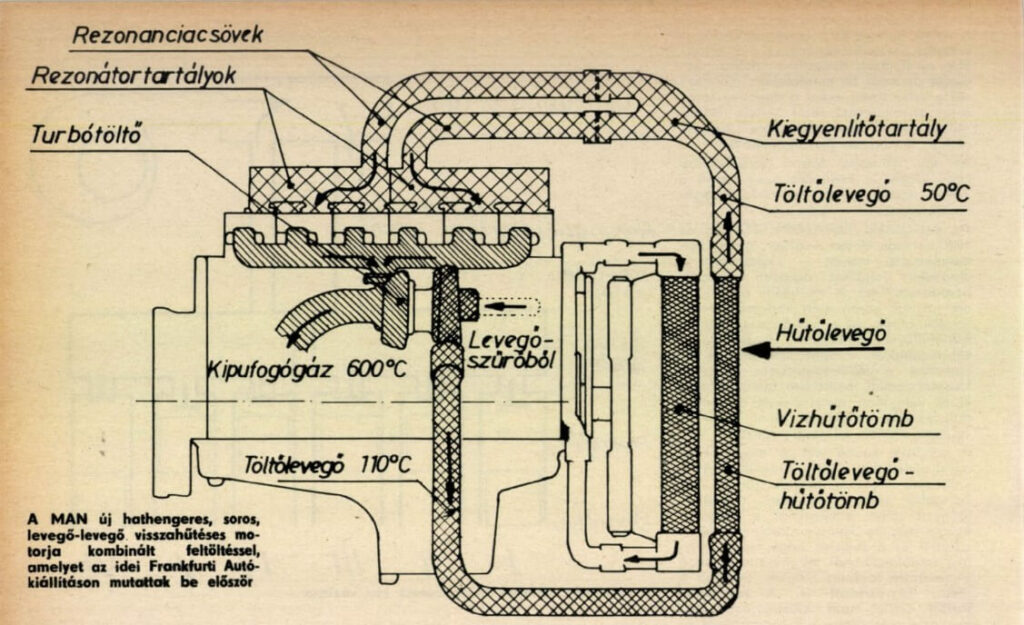
At higher revs, the picture changes radically as the piston rushes relative to the swing, so that the air at the end of the piston's intake stroke no longer reaches the opening of the intake valve, or is near the end of the moment when the air accelerated by the swing tries to squeeze into the cylinder.
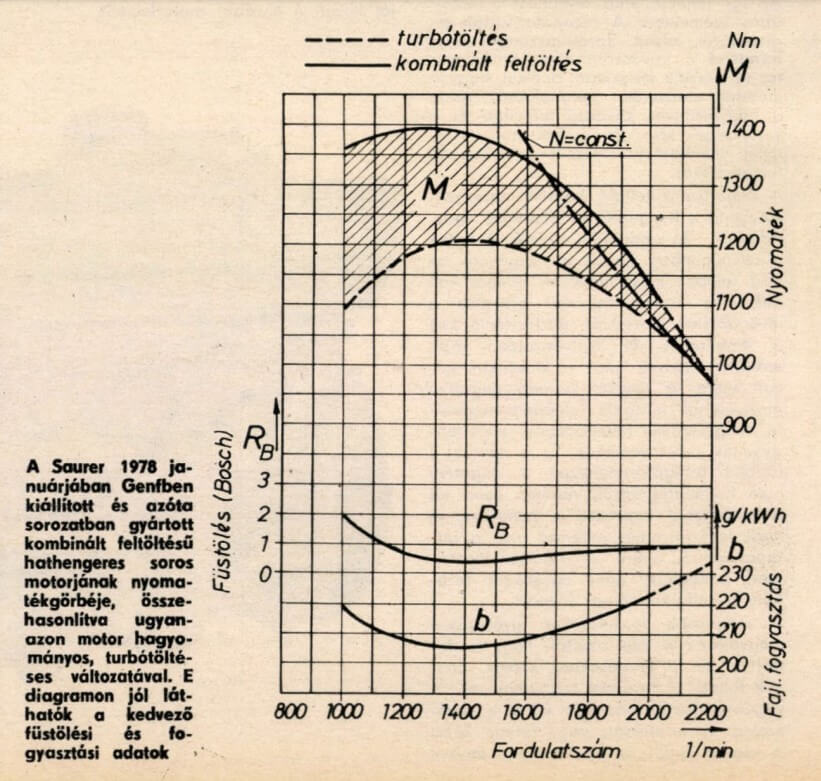
At this point, the intake valve has a smaller flow cross-section and does not allow this extra pressure to enter, so its energy cannot be used after the valve closes. Having said that, it is clear that if no changes are made to the tubes fitted to each cylinder individually, the delayed air movement will only consume energy but will not provide the required amount of air at the higher rpm.

This is why the so-called resonator tanks had to be installed. The idea is that 3-4 cylinders are connected to a single resonator tank. Here, the oscillation is not performed in a single tube, but in the resonator tank and the gas flowing in the tube together. This also means that the combined action of several cylinders can be taken into account for an optimal design. At low speeds, around and below the resonance speed, the situation does not change significantly compared to what has just been said.
But the change at high revs is fundamental. In this case, we have just established that the delayed oscillation does not reach the opening of the intake valve. Now, however, the excess pressure is not lost, but is retained in the resonator tank, and this air movement even precedes the opening of the intake valve of the next cylinder. The situation now is that the high pressure of the air which has already been excited by one piston now flows into the other cylinder at high speed, almost pushing the piston ahead of it. This piston therefore has to do very little work during the first half of the intake stroke, most of it being taken over by the movement of the air excited by the previous piston.
A further result of this changed swing phase is that the high-pressure fresh air flows into the cylinder when the intake valve is opened, i.e. when the exhaust valve is still open to facilitate the so-called flushing. Obviously, this situation will result in an increase in flush air at high revs. However, it is also the case that the relative amount of air required for combustion (fill factor) decreases, partly as a result of the increase in the amount of flushing air and partly because of the fact that the pressure maximum, the relative amount of air required for combustion, decreases in the second phase of piston movement, when the intake valve is already closed.
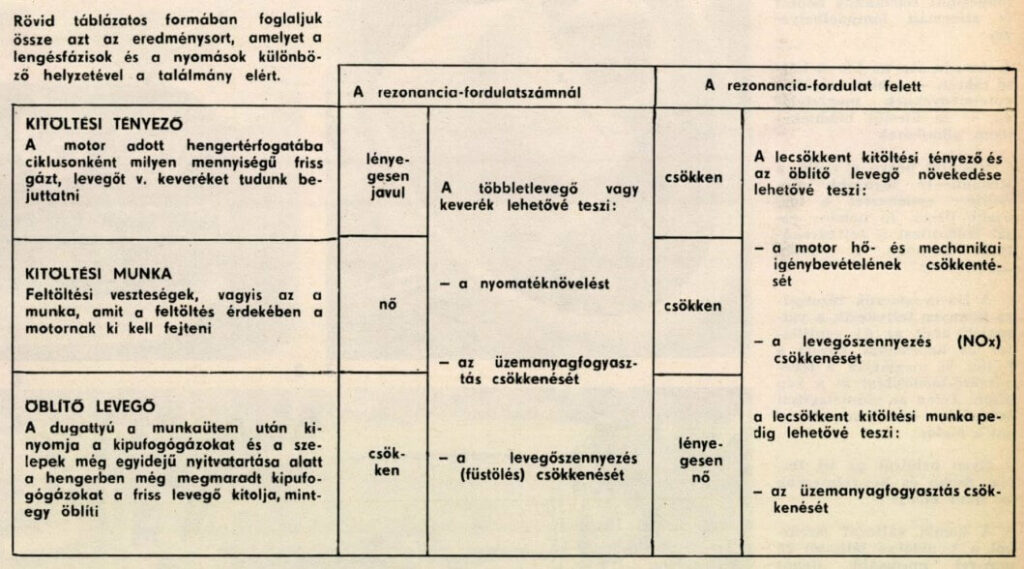
The invention of the motorcycle experts of the AUTO INDUSTRIAL RESEARCH INSTITUTE is protected by patents in nearly 30 countries. After an initial cautious reception, the pace has picked up!
After RÁBA, MAN, VOLVO and SAURER of Switzerland, North American and Japanese truck manufacturers have ordered the use of combined charging on their engines. Car engine manufacturers also got involved, with ALPINA, a manufacturer of special cars, being the first to introduce the technology on the market with its petrol car, but other diesel and petrol cars will soon be using the technology. In the meantime, concrete data and diagrams of the implementation illustrate the path taken so far.
The invention is of great importance for today's motor problems. However, the inventors themselves stress that it is not a "panacea", a "cure" for all motor problems.
The most optimal applications are being explored and adapted to specific engine types. But one thing is certain: in order to ensure that classic internal combustion engines operate economically and in line with requirements and that engine production prospers in the next 10-15 years, a combination of turbocharging and resonance charging, i.e. combined charging, will be indispensable!
DR KISS GYŐZ
the Road Transport
Scientific Research Institute
Deputy Scientific Director